Table of Contents
ToggleIntroduction
In recent years, derma rollers have surged in popularity within the skincare community, becoming a staple in both professional treatments and at-home skincare routines. These handheld devices, utilizing high-quality metals in derma roller manufacturing, are equipped with numerous fine microneedles that create micro-injuries on the skin. This process stimulates collagen production and enhances the absorption of topical treatments, leading to improved skin texture and a more youthful appearance. The choice of metals in derma roller manufacturing significantly impacts the effectiveness and durability of these devices, making informed selections crucial for optimal results.
Central to the effectiveness and safety of these devices is the choice of metals used in their construction. The materials chosen not only impact the durability and performance of the derma rollers but also play a crucial role in ensuring user safety and hygiene. This article delves into the various metals in derma roller manufacturing, exploring their benefits, the technologies behind their production, and important considerations for consumers seeking to optimize their skincare regimen.
Understanding Derma Rollers
What is a Derma Roller?
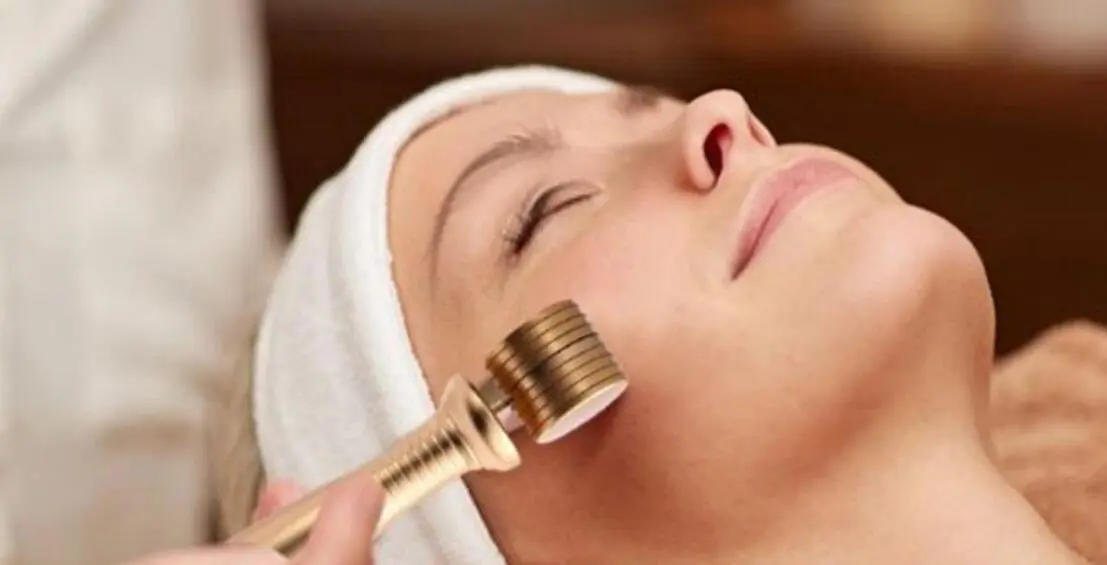
A derma roller is a sophisticated skincare tool designed to enhance the texture and appearance of the skin. It consists of a cylindrical handle attached to a roller covered with fine microneedles, typically ranging in length from 0.2 mm to 3.0 mm. When rolled over the skin, these microneedles create controlled micro-injuries, prompting the body’s natural healing response. This process results in increased collagen production, leading to firmer, more elastic skin. Additionally, the micro-injuries facilitate better absorption of serums and other topical treatments, making them more effective.
The versatility of derma rollers makes them suitable for various skin concerns, including fine lines, wrinkles, acne scars, and uneven texture. They can be used on different areas of the body, including the face, neck, and even the scalp to promote hair growth. However, the quality of the derma roller is paramount to achieving the desired results safely and effectively.
The Importance of Metal in Derma Roller Manufacturing
The materials used in derma rollers significantly influence their performance and safety. Metal is a key component, particularly for the needles and handles. High-quality metals ensure durability, hygiene, and effectiveness, making it essential for consumers to understand their options.
When it comes to the needles, the choice of metal impacts their sharpness and precision. For instance, stainless steel and titanium are commonly used due to their ability to maintain derma roller needle sharpness over time and resist corrosion. This is crucial for achieving optimal microneedling results, as dull needles can cause unnecessary discomfort and may not penetrate the skin effectively.
Moreover, the handle material also plays a significant role in user experience. Metal handles often provide a more sturdy and ergonomic grip compared to plastic alternatives, which can feel flimsy and less reliable. A well-designed metal handle enhances control during use, allowing for precise application.
Hygiene is another critical consideration. Metals such as stainless steel and titanium are easier to sterilize, minimizing the risk of infections. This is particularly important as the microneedling process involves creating micro-wounds on the skin. Choosing a derma roller made from high-quality metals can significantly reduce the likelihood of adverse reactions or complications.
In summary, understanding the various metals in derma roller manufacturing is crucial for making informed decisions. Consumers should consider the benefits and drawbacks of each metal type when selecting a derma roller, ensuring they choose a device that meets their skin care needs while prioritizing safety and effectiveness.
Types of Metals Used in Derma Roller Manufacturing
1. Stainless Steel Metals in Derma Roller Manufacturing
Properties and Benefits
Stainless steel is the most commonly used metal in derma roller manufacturing due to its favorable properties. This versatile material has earned its place as a preferred choice for various reasons:
- Durability: One of the standout features of stainless steel is its remarkable durability. It can withstand significant wear and tear, making it ideal for repeated use in microneedling procedures. The robust nature of stainless steel ensures that derma rollers maintain their integrity even after extensive application.
- Corrosion Resistance: Stainless steel’s inherent resistance to rust and corrosion is crucial for tools that come into contact with the skin. Exposure to moisture and various skincare products can lead to degradation in lower-quality materials. However, stainless steel remains unaffected, ensuring the longevity of the device and consistent performance over time.
- Hygiene: Maintaining hygiene is paramount in skincare, especially when dealing with devices that create micro-wounds on the skin. Stainless steel is easy to sterilize, which is crucial for preventing infections and maintaining skin health. Proper sterilization helps minimize the risk of introducing bacteria or other pathogens into the skin, which can lead to complications.
Applications in Derma Rollers
In derma rollers, stainless steel is typically used for both the microneedles and the handles. The sharpness and strength of stainless steel needles allow for effective penetration without excessive discomfort. When designed correctly, these needles can create the necessary micro-injuries to stimulate collagen production while minimizing pain for the user.
Moreover, stainless steel handles provide a sturdy and reliable grip, contributing to better control during application. The weight and feel of a stainless steel handle can enhance the overall user experience, making it easier to maneuver the roller across different areas of the skin.
2. Titanium Metals in Derma Roller Manufacturing
Properties and Benefits
Titanium has become increasingly popular in the skincare industry, particularly for high-end derma rollers. Its key properties make it an attractive option for consumers and professionals alike:
- Hypoallergenic Nature: Unlike some metals that may cause allergic reactions, titanium is biocompatible and less likely to irritate sensitive skin types. This characteristic is especially important for individuals who have a history of allergies or skin sensitivities, ensuring a safer microneedling experience.
- Lightweight: Titanium handles are typically lighter than those made of stainless steel, enhancing user comfort and control during application. The reduced weight minimizes hand fatigue, allowing for prolonged use without discomfort. This is particularly beneficial for estheticians and professionals who perform multiple treatments in a single day.
- Durability: Titanium is highly resistant to wear, corrosion, and impact, ensuring the longevity of the device. Its robust nature means that titanium derma rollers can withstand the rigors of professional use without compromising performance, making them a worthwhile investment for both professionals and serious skincare enthusiasts.
Applications in Derma Rollers
Titanium is often used in professional-grade derma rollers, particularly those designed for sensitive skin. The combination of its strength and lightweight nature provides an excellent user experience. The needles made from titanium are not only sharp but also maintain their effectiveness over extended use. This ensures that users can achieve optimal results while minimizing discomfort.
Additionally, the sleek, modern aesthetic of titanium handles appeals to many consumers, making these derma rollers not just functional but also visually appealing.
3. Aluminum Metals in Derma Roller Manufacturing
Properties and Benefits
Aluminum is another metal used in the manufacturing of derma rollers, particularly for the handles. Its key benefits include:
- Lightweight: Aluminum handles are easy to maneuver, which is particularly beneficial for prolonged use. This lightweight nature allows users to navigate the device easily across various areas of the skin, reducing strain during application.
- Cost-Effectiveness: Aluminum is generally more affordable than stainless steel and titanium, making it a popular choice for budget-friendly products. This cost-effectiveness makes it accessible to a wider audience, allowing more people to incorporate derma rolling into their skincare routines.
Applications in Derma Rollers
While aluminum is not typically used for microneedles due to its lower durability, it can be effective for the handles of derma rollers. Some users appreciate the lighter feel of aluminum, especially during longer sessions, as it reduces fatigue and enhances comfort.
However, consumers need to be aware that aluminum handles may not offer the same level of durability as stainless steel or titanium. While they are suitable for home use, professionals may prefer stainless steel or titanium options for their added longevity and performance.
Conclusion
In summary, understanding the various metals in derma roller manufacturing is crucial for making informed decisions. Each metal offers unique properties and benefits that can significantly impact the effectiveness and safety of the device.
Choosing a derma roller made from high-quality materials, such as stainless steel or titanium, can enhance your skincare routine and ensure optimal results. For those on a budget, aluminum options provide a lightweight and accessible alternative. Ultimately, being aware of the differences in metals will empower consumers to select the best derma roller for their individual needs.
Manufacturing Processes for Metals in Derma Roller Manufacturing
The manufacturing processes for metals used in derma rollers are crucial for producing high-quality tools that ensure safety, effectiveness, and longevity. Understanding these processes can help consumers appreciate the craftsmanship involved in creating their skincare devices. Here, we explore several key manufacturing methods used in the production of metal derma rollers, highlighting their benefits and significance.
1. CNC Machining in Metal Derma Roller Manufacturing
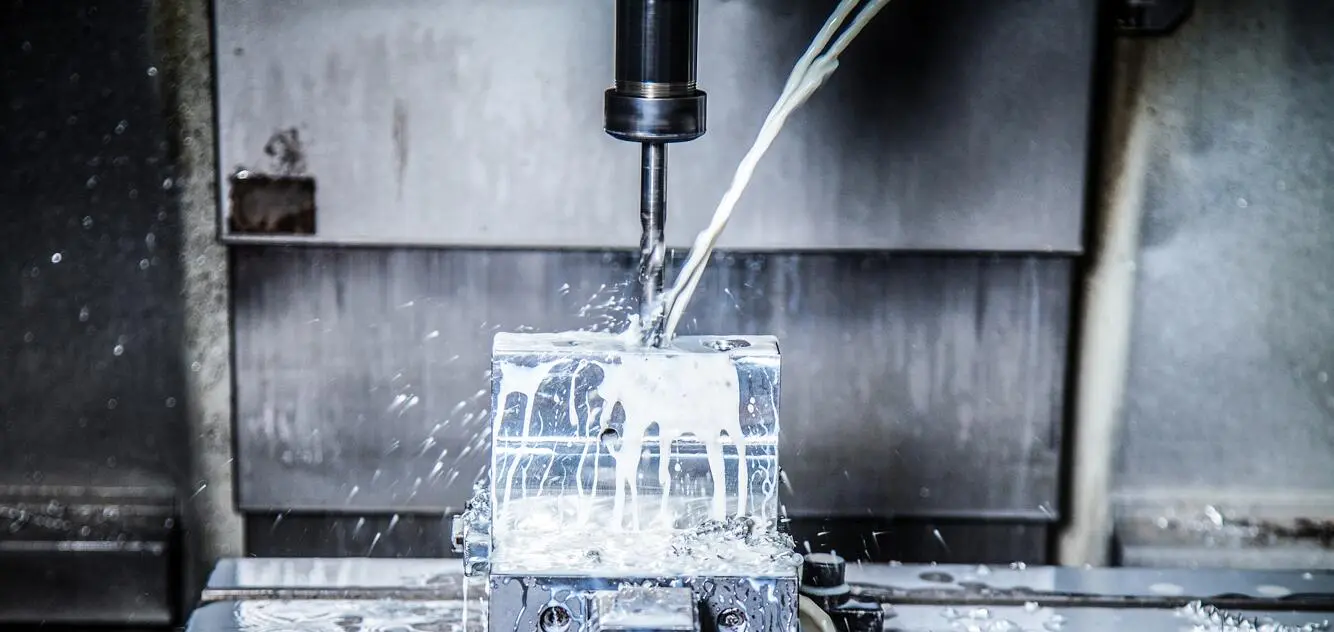
CNC (Computer Numerical Control) machining is a highly precise manufacturing process that utilizes computer software to control machine tools. This technology has revolutionized how metal components are shaped and cut, making it an essential method for producing derma rollers.
Benefits of CNC Machining
- Precision: One of the standout features of CNC machining is its ability to produce parts with remarkable accuracy. The computer-controlled nature of this process allows for minimal variations in dimensions, ensuring that each derma roller is manufactured to exact specifications. This precision is critical in creating sharp microneedles that penetrate the skin effectively without causing excessive discomfort.
- Complex Designs: CNC machining enables microneedle derma roller manufacturers to create intricate designs that may be challenging to achieve through traditional manufacturing methods. For instance, the ability to create unique patterns on the handles or specific configurations for the microneedles can enhance both functionality and aesthetics.
- Efficiency: CNC machines can operate continuously, significantly increasing production efficiency. This capability allows manufacturers to produce large quantities of derma rollers without sacrificing quality. Furthermore, because CNC machines can be programmed to perform multiple tasks, they streamline the manufacturing process and reduce turnaround times.
2. Laser Cutting in Metal Derma Roller Manufacturing
Laser cutting is another advanced technology widely used to manufacture metal handle derma rollers. This process involves using focused laser beams to cut or engrave materials with high accuracy.
Benefits of Laser Cutting
- Clean Edges: One of the primary advantages of laser cutting is its ability to produce smooth and clean edges. This quality is particularly essential for the sharp microneedles found in derma rollers. A clean edge ensures that the needles can penetrate the skin effectively, enhancing the overall efficacy of the device.
- Speed: The laser cutting process is notably fast, which allows for quicker turnaround times in production. This speed is especially beneficial in a competitive market where timely delivery is crucial. Manufacturers can produce more units in less time, meeting the demands of both retail and professional markets.
- Flexibility: Laser cutting offers flexibility in design adjustments. If a manufacturer needs to change the design or specifications of a derma roller, laser cutting can be easily adjusted without significant setup changes. This adaptability enables manufacturers to respond quickly to consumer preferences and market trends.
3. Forging in Metal Derma Roller Manufacturing
Forging is a traditional manufacturing process that involves shaping metal using compressive forces. This method is often used to create robust and durable metal handles for derma rollers.
Benefits of Forging
- Strength: One of the primary benefits of forging is that it significantly increases the strength of the metal. The compressive forces applied during the forging process align the metal’s internal grain structure, making the resulting components less likely to break or deform under stress. This strength is vital for handles that must endure repeated use.
- Durability: Forged metal parts generally exhibit better fatigue resistance compared to those created through casting or machining. This durability ensures that the handles of derma rollers can withstand regular use without showing signs of wear or failure.
- Consistency: Forging allows for uniformity in the production of multiple components. This consistency is crucial for manufacturers aiming to produce derma rollers that meet high-quality standards. Each handle can be produced to the same specifications, ensuring that every unit performs reliably.
4. Surface Treatments in Metal Derma Roller Manufacturing
Surface treatments, such as anodizing and electroplating, play a vital role in enhancing the properties of metal handles in derma rollers. These treatments improve both functionality and aesthetics.
Benefits of Surface Treatments
- Corrosion Resistance: One of the significant benefits of surface treatments is that they enhance the metal’s resistance to corrosion. Anodizing, for example, creates a protective oxide layer on the surface of aluminum or other metals, prolonging the lifespan of the device. This resistance is essential for skincare tools that may come into contact with moisture and various products.
- Aesthetic Appeal: Surface treatments can enhance the visual appeal of derma rollers, offering various finishes and colors that can attract consumers. Aesthetics play a significant role in skincare products, and a well-designed, visually appealing derma roller can increase consumer interest and sales.
- Ease of Cleaning: Smooth, treated surfaces are easier to clean, which is critical for maintaining hygiene. Given that derma rollers create micro-wounds on the skin, it is essential to keep these tools free from bacteria and contaminants. Surface treatments facilitate better cleaning practices, ensuring that users can maintain their derma rollers effectively.
Conclusion of Metals in Derma Roller Manufacturing
The manufacturing processes for metals in derma roller manufacturing are critical in producing high-quality, effective, and safe skincare tools. Each method, from CNC machining to laser cutting, forging, and surface treatments, contributes unique benefits that enhance the performance and durability of derma rollers.
Understanding these processes not only helps consumers appreciate the craftsmanship involved in creating their skincare devices but also empowers them to make informed decisions when selecting the right derma roller for their needs. By prioritizing quality manufacturing, users can enhance their skincare routines and achieve optimal results.
The Impact of Metal Choice on Derma Roller Effectiveness
Sharpness and Precision in Metals for Derma Roller Manufacturing
The type of metal used in the microneedles significantly impacts their sharpness and precision, which are critical factors for the effectiveness of derma rollers. High-quality materials such as stainless steel and titanium are widely favored for their ability to produce sharp, effective needles that can penetrate the skin at the optimal angle.
- Stainless Steel: This metal is renowned for its hardness and ability to maintain a sharp edge over time. The sharpness of stainless steel needles allows for precise micro-penetrations that stimulate collagen production without excessive pain or trauma to the skin. Properly designed stainless steel needles can create micro-injuries that trigger the skin’s natural healing processes, leading to rejuvenated skin and improved texture.
- Titanium: Similarly, titanium is an excellent choice for microneedles due to its inherent strength and resistance to corrosion. The lightweight nature of titanium, combined with its sharpness, allows for effortless movement across the skin while ensuring effective penetration. Titanium needles can provide a smoother experience and are often recommended for sensitive skin types due to their hypoallergenic properties.
On the contrary, using dull or low-quality needles made from inferior metals can lead to discomfort and ineffective treatments. Dull needles may drag or pull at the skin rather than glide smoothly, which can result in irritation, inflammation, or even injury. Therefore, investing in derma rollers made from high-quality metals is essential for achieving the best results.
Durability and Longevity of Metals in Derma Roller Manufacturing
Durability is another crucial factor influenced by the choice of metal in derma roller manufacturing. The metal used must be able to withstand regular use without degrading over time. High-quality metals like stainless steel and titanium not only resist wear but also maintain their effectiveness and sharpness, allowing users to benefit from their investment in the long term.
- Stainless Steel: Known for its robust nature, stainless steel is highly resistant to wear and tear. This durability means that derma rollers made from stainless steel can be used repeatedly without the risk of the needles bending or losing their sharpness. Regular maintenance and cleaning can further enhance the longevity of these devices.
- Titanium: In addition to being lightweight, titanium is exceptionally durable. Its resistance to corrosion and fatigue makes it an ideal material for professional-grade derma rollers. Even with frequent use, titanium needles can maintain their integrity, ensuring consistent results throughout their lifespan.
Choosing a derma roller crafted from durable metals can significantly impact its longevity and effectiveness. Consumers should prioritize products that highlight the quality of their materials, as this often reflects their commitment to performance and user satisfaction.
User Experience with Metals in Derma Roller Manufacturing
The overall user experience is heavily influenced by the weight and feel of the metal handle used in derma rollers. Ergonomically designed metal handles provide a comfortable grip and better control, which is essential for achieving precise applications.
- Ergonomics and Comfort: Handles made from stainless steel or titanium are often designed with user comfort in mind. The solid feel of metal can inspire confidence during use, allowing individuals to focus on the treatment rather than worrying about the device’s stability. In contrast, plastic handles may feel flimsy and less reliable, potentially leading to a less satisfying user experience.
- Control and Precision: A well-balanced metal handle enhances control, allowing users to navigate the roller smoothly across different areas of the skin. This precision is vital for targeting specific concerns, such as fine lines or acne scars. A sturdy metal handle can also reduce hand fatigue during longer sessions, making the experience more enjoyable and effective.
In summary, the choice of metals in derma roller manufacturing plays a significant role in shaping user experience. High-quality metals contribute to sharpness, durability, and comfort, all of which are essential for effective skincare treatments.
Considerations When Choosing a Metal Handle Derma Roller
Skin Sensitivity and Metals in Derma Roller Manufacturing
For individuals with sensitive skin, the choice of metal becomes particularly important. Different metals can have varying effects on the skin, and selecting the right material can help minimize the risk of allergic reactions or irritation.
- Titanium: Often recommended for its hypoallergenic properties, titanium is an excellent choice for those with sensitive skin. Its biocompatibility means that it is less likely to cause adverse reactions, making it suitable for a wider range of users.
- Stainless Steel: While stainless steel is generally safe for most skin types, some individuals may have specific metal allergies that could lead to irritation. Users should be mindful of their skin sensitivities and opt for titanium if they have concerns about potential reactions.
When choosing a derma roller, consumers should consider their skin type and any known allergies to ensure they select a product that is both safe and effective for their skincare needs.
Maintenance and Care for Metals in Derma Roller Manufacturing
Proper maintenance of a derma roller is crucial for prolonging its lifespan and ensuring safety during use. Users should follow the manufacturer’s guidelines for cleaning and sterilizing metal components.
- Cleaning Routine: Regular cleaning helps prevent bacterial growth and maintains the effectiveness of the microneedles. After each use, derma rollers should be cleaned with alcohol or a gentle antibacterial solution. This practice not only keeps the device hygienic but also extends its lifespan by preventing corrosion and degradation.
- Storage: Proper storage is equally important. Derma rollers should be kept in a clean, dry place to avoid exposure to contaminants. Some manufacturers provide protective cases that help shield the roller from dirt and damage, which can be an excellent investment for maintaining quality.
Brand Reputation and Metals in Derma Roller Manufacturing
When selecting a derma roller, choosing a reputable brand is essential. Derma roller companies that prioritize quality materials and transparent manufacturing processes often produce more reliable and effective products.
- Research and Reviews: Consumers should look for brands with positive reviews and testimonials. Insights from other users can provide valuable information about the effectiveness and durability of the product. Additionally, brands that are transparent about their manufacturing processes and materials used are often more trustworthy.
- Warranty and Customer Support: Reputable brands usually offer warranties or guarantees on their products, reflecting their confidence in the quality of their manufacturing. Strong customer support is also an indicator of a brand’s commitment to consumer satisfaction, making it easier for users to seek assistance if needed.
In conclusion, selecting a high-quality metal handle derma roller involves considering several factors, including the type of metal, skin sensitivity, maintenance practices, and brand reputation. By prioritizing these considerations, consumers can make informed choices that enhance their skincare routines and achieve optimal results.
Sustainability in Metal Derma Roller Manufacturing
As the skincare industry grows, so does the awareness of its environmental impact. Consumers are increasingly prioritizing eco-friendly products, prompting manufacturers to adopt sustainable practices in metal derma roller manufacturing. This shift not only benefits the planet but also aligns with the values of a growing demographic of environmentally conscious consumers.
Eco-Friendly Practices in Derma Roller Manufacturing
Using Recyclable Materials
One of the primary strategies manufacturers employ to promote sustainability is the use of recyclable materials. Metals such as stainless steel and aluminum are highly recyclable, making them excellent choices for eco-friendly products.
- Stainless Steel: This metal is not only durable and corrosion-resistant, but it is also recyclable. When a stainless steel derma roller reaches the end of its life cycle, it can be melted down and repurposed into new products. This recycling process reduces the demand for virgin materials, conserving resources and minimizing environmental impact.
- Aluminum: Similar to stainless steel, aluminum is lightweight, durable, and infinitely recyclable without loss of quality. The energy required to recycle aluminum is significantly less than that needed for primary aluminum production, leading to a smaller carbon footprint. Manufacturers who use aluminum in their derma rollers can effectively contribute to a circular economy.
By choosing derma rollers made from these recyclable metals, consumers can play a part in reducing waste and promoting sustainability. When these products are disposed of properly, they can be reincorporated into the manufacturing cycle, minimizing environmental impact.
Minimizing Waste in Metals in Derma Roller Manufacturing
Sustainable manufacturing practices extend beyond material choice. Efficient production processes that minimize waste are equally crucial for reducing the overall environmental footprint.
- Lean Manufacturing Techniques: Many manufacturers are adopting lean manufacturing principles, which focus on optimizing processes to reduce waste. This includes careful planning and execution of production methods to ensure that excess materials are minimized. For instance, using advanced cutting techniques like CNC machining can maximize the use of raw materials, reducing scrap.
- Quality Control: Implementing strict quality control measures ensures that products meet high standards, reducing the likelihood of defects that result in waste. By producing high-quality derma rollers that last longer, manufacturers can decrease the frequency of replacements, further contributing to sustainability.
- Sustainable Supply Chains: Many companies are also focusing on creating sustainable supply chains by sourcing materials from ethical suppliers. This approach ensures that the metals used in derma roller manufacturing are not only high-quality but also sourced responsibly, minimizing environmental impact throughout the supply chain.
The Future of Sustainable Derma Rollers
The trend toward sustainability in metal derma roller manufacturing is poised to grow as consumers increasingly demand eco-conscious products. Several factors will influence this evolution in the industry.
Consumer Awareness and Demand
As awareness of environmental issues rises, consumers are becoming more discerning about the products they purchase. This shift in consumer behavior is prompting brands to prioritize sustainability in their offerings.
- Transparency: Brands that are transparent about their manufacturing processes and material sourcing are more likely to attract environmentally conscious consumers. By openly communicating their sustainability efforts, companies can build trust and loyalty among their customer base.
- Eco-Certifications: As consumers look for tangible evidence of a brand’s commitment to sustainability, eco-certifications will become increasingly important. Manufacturers who can provide certifications or third-party endorsements regarding their eco-friendly practices may gain a competitive edge in the market.
Technological Advancements
The future of sustainable derma rollers will also be shaped by technological advancements in manufacturing processes. Innovations that enhance efficiency and reduce environmental impact are already being integrated into production lines.
- 3D Printing: This technology holds the potential to revolutionize the manufacturing of metal components for derma rollers. 3D printing allows for precise production with minimal material waste. Moreover, it enables the creation of complex designs that may not be achievable through traditional methods.
- Smart Manufacturing: The integration of IoT (Internet of Things) technologies into manufacturing processes can lead to more efficient operations. Smart factories can monitor energy consumption, waste generation, and material usage in real-time, allowing for continuous improvements in sustainability.
The Importance of Metals in Derma Roller Manufacturing
Understanding the impact of metals in derma roller manufacturing is essential for consumers seeking to make informed choices. Metals play a vital role in the manufacturing of derma rollers, influencing their effectiveness, safety, and user experience. By prioritizing recyclable materials and efficient manufacturing processes, brands can significantly reduce their environmental impact.
Investing in a quality derma roller made from high-quality metals can enhance your skincare routine while supporting sustainable practices. As the skincare industry evolves, staying updated on advancements in metal usage and manufacturing technologies will be essential for both manufacturers and consumers.
Round Up
The shift toward sustainability in metal derma roller manufacturing is not just a trend; it is a necessary evolution in the skincare industry. As consumers demand more eco-friendly products, manufacturers must adapt by prioritizing recyclable materials, minimizing waste, and adopting innovative technologies.
Ultimately, making informed choices about the products we use can contribute to a more sustainable future. By selecting derma rollers crafted with care for the environment, consumers can play an active role in promoting sustainability in the beauty industry. This conscious approach not only benefits our skin but also helps protect our planet for future generations.
FAQs Regarding Metals in Derma Roller Manufacturing
1. What metals are commonly used in derma roller manufacturing?
The most commonly used metals in derma roller manufacturing are stainless steel, titanium, and aluminum. Each metal offers unique properties that enhance the effectiveness and durability of the rollers.
2. Why is stainless steel preferred for derma rollers?
Stainless steel is preferred for derma rollers due to its durability, corrosion resistance, and ability to maintain sharpness. It’s also easy to sterilize, ensuring hygiene during use.
3. How does titanium benefit derma roller users?
Titanium is lightweight, hypoallergenic, and highly resistant to wear and corrosion. These qualities make it ideal for sensitive skin types and enhance user comfort during treatment.
4. What is the importance of microneedle sharpness in derma rollers?
Microneedle sharpness is crucial for effective treatment. Sharp needles create precise micro-injuries that stimulate collagen production and improve the absorption of skincare products while minimizing discomfort.
5. How do metals in derma roller manufacturing affect durability?
The choice of metals significantly impacts the durability of derma rollers. High-quality metals like stainless steel and titanium withstand regular use without degrading, ensuring the device lasts longer.
6. Can derma rollers made from aluminum be effective?
Yes, aluminum can be used for derma roller handles due to its lightweight nature and cost-effectiveness. However, it may not be as durable as stainless steel or titanium for the microneedles.
7. How can consumers ensure they are choosing eco-friendly derma rollers?
Answer: Consumers can look for derma rollers made from recyclable metals, such as stainless steel and aluminum, and check for brands that prioritize sustainable manufacturing practices.
8. What maintenance is required for metal derma rollers?
Regular cleaning with alcohol or a gentle antibacterial solution is essential after each use. Proper storage in a clean, dry place also helps maintain the device’s integrity and hygiene.
9. How do advancements in manufacturing technologies impact derma rollers?
Innovations like CNC machining and 3D printing enhance the precision and efficiency of derma roller manufacturing, leading to better quality products with less waste.
10. Why should consumers stay informed about metals in derma roller manufacturing?
Staying informed allows consumers to make educated choices about their skincare tools. Understanding the impact of different metals on effectiveness, safety, and sustainability can lead to better skincare outcomes and promote eco-friendly practices.