Table of Contents
ToggleManufacturing Microneedles on a Derma Roller: Process and Materials
Learn about how microneedles on a derma roller are processed by derma roller manufacturers, including the materials used, the design process, precision engineering, sterilization techniques, and the role of technology. Understanding this process will help you appreciate the quality and safety of derma rollers, benefiting your skincare routine.
Discover the challenges in manufacturing microneedles, such as achieving precision, material selection, design complexities, sterilization, quality control, and environmental considerations. By learning about these challenges, you will gain insight into the meticulous process behind derma roller production and appreciate the importance of quality standards in skincare devices.
Key Points
- Materials Used in Derma Roller Microneedles
- The Design Process of Microneedles
- Precision Engineering in Microneedle Manufacturing
- Sterilization Techniques for Microneedles
- The Role of Technology in Microneedle Fabrication
- Common Challenges in Manufacturing Microneedles
- Environmental Considerations in Microneedle Production
- Future Trends in Derma Roller Microneedle Manufacturing
What is a Derma Roller and its Uses?
A derma roller is a skincare device that features a handle with a cylindrical drum attached at one end. This drum is installed with a variety of tiny, great needles, referred to as microneedles. The primary objective of a derma roller is to perform a process called microneedling, which entails rolling the tool throughout the skin to produce regulated micro-injuries. These micro-injuries advertise collagen manufacturing and enhance the absorption of skin care products.
Derma rollers are commonly used for various skin problems, including:
Skin Problem | Impact of Microneedling |
---|---|
Acne Marks | Lowers the appearance of marks by boosting collagen |
Great Lines and Wrinkles | Improves skin texture and decreases wrinkles |
Hyperpigmentation | Lightens dark areas via skin regrowth |
Stretch Marks | Minimizes the look of stretch marks |
Loss of hair | Promotes hair growth by raising blood flow |
The effectiveness of a derma roller mostly depends on the quality and style of the microneedles. Manufacturers usually make the microneedles on a derma roller from surgical-grade stainless steel or titanium, ensuring both resilience and safety for skin contact. The production procedure of these microneedles includes accuracy engineering to make sure each needle is sharp enough to penetrate the skin without causing unnecessary damage.
Derma rollers are readily available in various needle sizes, normally ranging from 0.2 mm to 2.5 mm, each serving various objectives. For instance, manufacturers generally utilize much shorter needles (0.2 mm–0.5 mm) for improving product absorption and addressing superficial skin concerns, while they use longer needles (1.0 mm–2.5 mm) for deeper skin issues such as severe acne scars and stretch marks.
In professional settings, skin specialists and aesthetic experts frequently utilize derma rollers. Nevertheless, manufacturers also design variations for home use. Despite the setting, it is important to follow proper sterilization and use guidelines to prevent issues such as infections or skin damages.
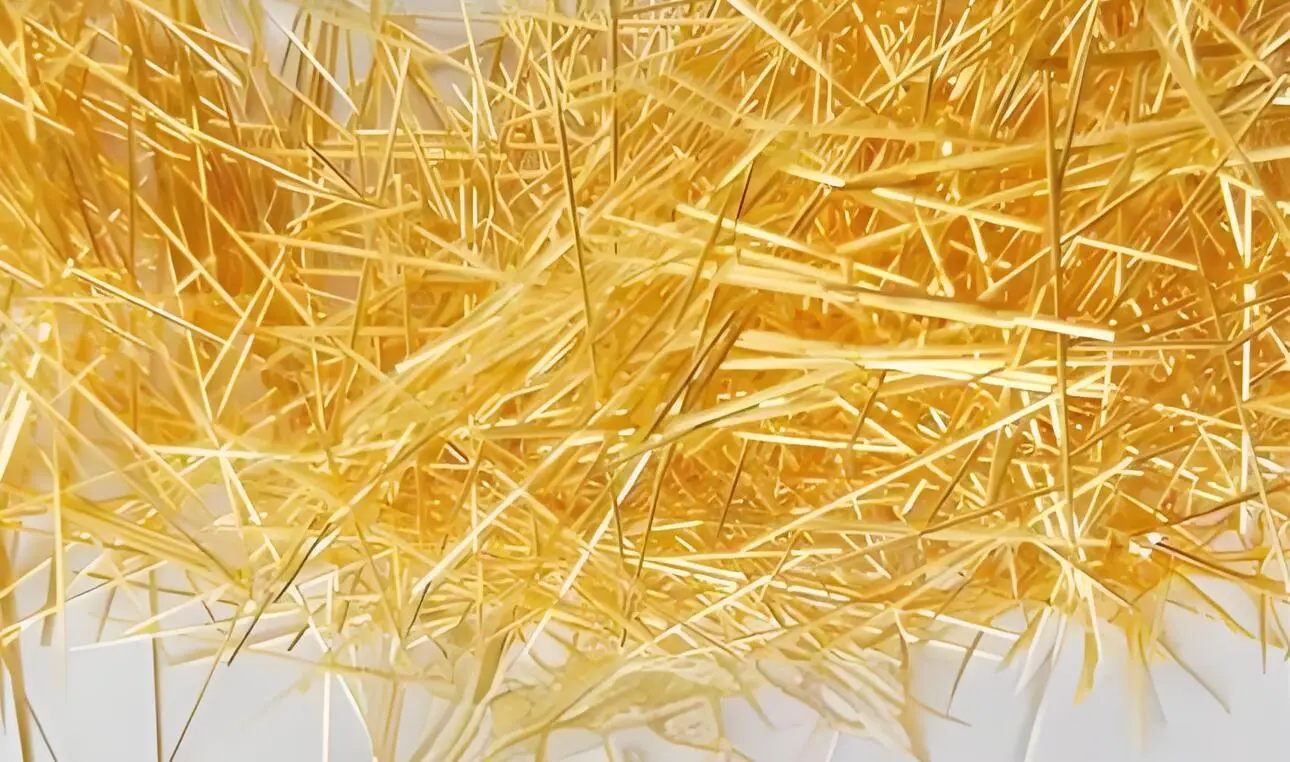
Materials Used in Microneedles On A Derma Roller
The Design Process of Microneedles
The style procedure of microneedles on a derma roller is a critical phase that guarantees the performance and security of the item. The process typically begins with conceptualization, where the key requirements such as size, diameter, and form of the microneedles are determined based upon their planned usage. For example, microneedles designed for face treatments might differ in specs compared to those meant for scalp treatments.
When the fundamental criteria are established, the next step is material selection. Commonly used materials consist of stainless-steel, titanium, and medical-grade polymers. These products are selected for their biocompatibility, durability, and ability to be precisely manufactured. Each material has its benefits; for instance, stainless steel is understood for its stamina and sharpness retention, while titanium is renowned for its lightweight and corrosion resistance.
The design phase likewise includes computer-aided layout (CAD) software application to develop detailed 3D designs of the microneedles. These designs enable for specific control over the microneedle dimensions, guaranteeing harmony in production. The CAD versions are then made to replicate different elements, such as skin penetration force, structural honesty, and user convenience. This action is critical in determining and mitigating prospective problems before relocating to physical prototyping.
Prototyping includes producing physical samples of the microneedles on a derma roller using strategies such as micro-molding, laser cutting, or electrochemical etching. These models go through rigorous screening to assess their efficiency in real-world conditions. Specifications such as infiltration depth, skin communication, and toughness are thoroughly examined. Comments from these tests inform any necessary modifications to the layout.
Throughout the layout procedure, regulatory compliance is a key consideration. Microneedle designs need to stick to medical tool guidelines and requirements, which differ by region. This includes making certain that the materials and manufacturing processes satisfy rigorous safety and efficacy requirements.
The following table summarizes a few of the crucial specifications thought about throughout the design process:
Criterion | Description |
---|---|
Size | It usually ranges from 0.2 mm to 2.5 mm, depending upon the application |
Diameter | Generally, between 50 micrometers and 200 micrometers |
Product | Stainless steel, titanium, and medical-grade polymers |
Shape | Cone-shaped, pyramidal, or round |
Production Techniques | Micro-molding, laser cutting, and electrochemical etching |
In recap, the style procedure of microneedles is a careful and multi-faceted strategy that combines material scientific research, engineering accuracy, and governing conformity to create a secure and reliable item.
Precision Engineering in Microneedle Manufacturing
The manufacturing of microneedles on a derma roller entails a high degree of accuracy to make sure that each microneedle is produced to exact specifications. This accuracy is essential for the safety and performance of the derma roller.
Among the primary methods utilized in microneedle manufacturing is micro-molding. This procedure includes developing mold and mildew that mirror the exact measurements and shape of the wanted microneedle. Products such as medical-grade polymers are then injected right into the mold and mildew under high pressure to create the microneedles. Micro-molding enables the manufacturing of microneedles with extremely fine ideas, which are essential for passing through the skin with very little discomfort.
An additional secret approach is laser cutting. For metal microneedles, such as those made from stainless-steel or titanium, laser cutting provides the accuracy required to form the microneedles properly. This strategy utilizes high-powered lasers to cut with the product, permitting the creation of exceptionally sharp and specific microneedles. The precision of laser cutting ensures that each microneedle keeps consistent dimensions and sharpness, which is critical for their efficiency.
Electrochemical etching is also employed, specifically for metal microneedles. This process includes making use of an electrolytic option to etch the steel to the desired shape and intensity. Electrochemical etching can create microneedles with very smooth surfaces, which helps reduce skin irritability throughout usage.
For silicon microneedles, photolithography and engraving techniques obtained from the semiconductor industry are usually utilized. These processes allow for the creation of microneedles with really exact geometries and high element ratios. Making use of such innovative methods ensures that the microneedles are both sturdy and efficient.
Quality control is an integral part of the accuracy of the design procedure. Each batch of microneedles undergoes rigorous screening and assessment to make certain that they fulfill stringent standards. Parameters such as length, diameter, and idea intensity are very carefully gauged, and any type of discrepancies from the requirements are dealt with instantly. This makes certain that every derma roller provides consistent performance and safety for the end user.
The function of accuracy engineering in microneedle manufacturing can not be overemphasized. It is this meticulous attention to detail that ensures the performance, security, and integrity of derma rollers in their various applications.
Sterilization Techniques for Microneedles On A Derma Roller
Ensuring the sterility of microneedles on a derma roller is an essential action in the production process of derma rollers. The key goal is to get rid of any kind of microorganisms that can trigger infections or various other damaging results upon use. Numerous sanitation strategies are used in the sector, each with its own benefits and restrictions. Below is a review of the most frequently used techniques:
Ethylene Oxide (EO) Sterilization
Ethylene oxide sterilization is an extensively utilized approach due to its efficiency in passing through the tiny gaps of microneedles. EO gas interferes with the DNA of microbes, guaranteeing a high level of sterility. The process involves revealing the microneedles to EO gas in a regulated atmosphere. A significant advantage of this approach is that it can disinfect at reasonably low temperature levels, which is beneficial for materials that are delicate or warm.
Gamma Radiation
Gamma radiation sanitation uses high-energy photons to ionize the mobile material of microorganisms, effectively eliminating them. This method is particularly efficient for bulk sanitation and is understood for its deep penetration capacities. Gamma radiation is a highly reputable approach, although it needs specialized tools and precautions because of the contaminated resource.
Autoclaving
Autoclaving is a steam sterilization method that utilizes high-pressure saturated vapor at temperature levels typically varying from 121 ° C to 134 °C. While very efficient, this approach is generally utilized for materials that can endure high temperature levels and dampness. The key constraint of autoclaving for microneedles is that it might not be ideal for all materials, especially those that are heat-sensitive.
Electron Beam Of Light Sanitation
Electron light beam (e-beam) sanitation uses high-energy electrons to disrupt the DNA of microorganisms. This approach is comparable to gamma radiation, but makes use of a different kind of energy. E-beam sterilization is useful as a result of its speed and the ability to manage the dosage of radiation much more precisely. It is typically utilized for items that call for quick turnaround times in the manufacturing process.
Sterilization Method | Advantages | Limitations |
---|---|---|
Ethylene Oxide (EO) | Effective at reduced temperature levels, penetrates tiny gaps | Needs aeration to eliminate recurring gas, long handling time |
Gamma Radiation | Deep penetration, suitable for mass sterilization | Needs specialized devices, security problems |
Autoclaving | Highly reliable, extensively available | Not appropriate for heat-sensitive materials |
Electron Light beam (e-beam) | Fast process, accurate dosage control | Minimal penetration depth, high initial cost |
Each sanitation technique has its own set of protocols and quality assurance steps to ensure the sterility of the microneedles. The choice of technique mostly depends on the product of the microneedles and the certain demands of the producer. A focus on sterility is vital to ensuring the security and effectiveness of derma rollers for scientific and consumer use.
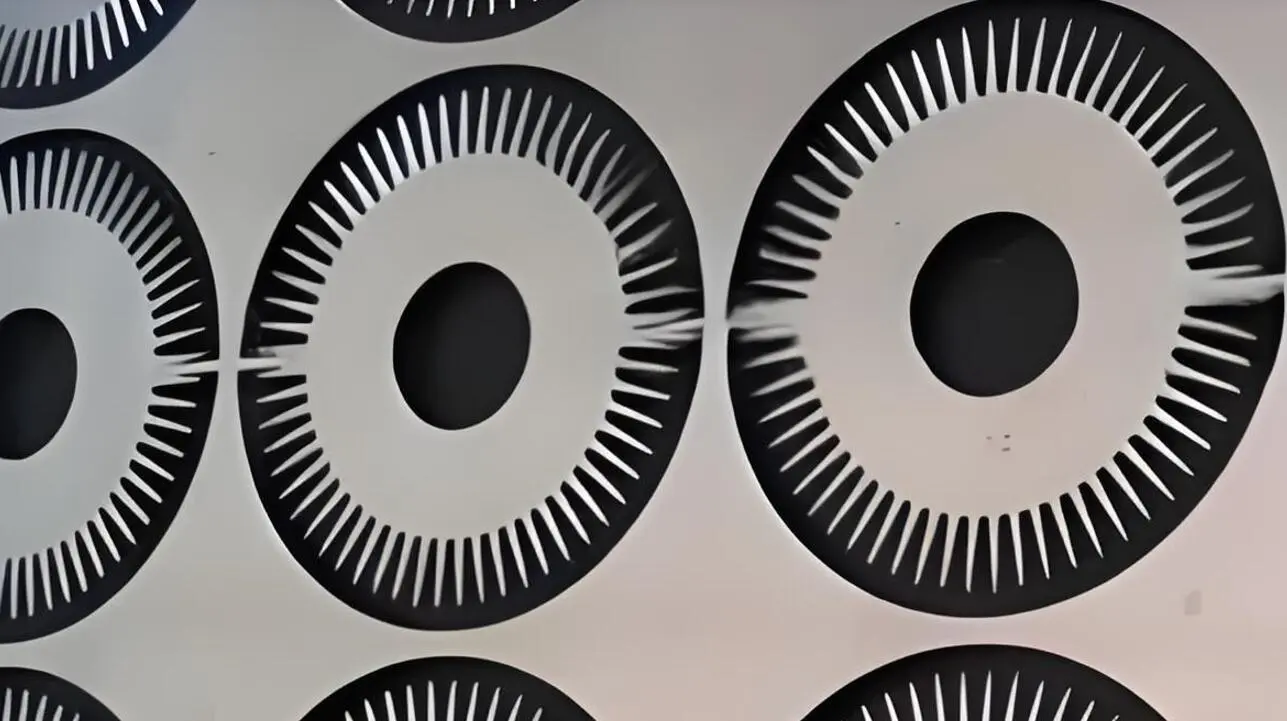
The Role of Technology in Microneedle Fabrication
The manufacture of microneedles for derma rollers has actually substantially gained from breakthroughs in innovation, which have boosted accuracy, efficiency, and consistency in manufacturing. A significant facet of this process involves making use of computer-aided design (CAD) software, which permits the careful planning and modeling of microneedle frameworks. This precision makes sure that each microneedle is crafted to precise requirements, enhancing its performance and safety.
Among the critical technologies employed in microneedle manufacturing is laser reducing. This approach uses high-powered lasers to reduce products with extreme precision, guaranteeing that each microneedle is uniform in dimension and shape. Laser cutting is particularly useful because of its capability to manage complex styles and its very little influence on the product’s structural honesty.
Furthermore, micro-molding methods are frequently utilized in the production of microneedles. These methods entail producing mold and mildew at a microscale that exactly specifies the form and size of the microneedles. The mold and mildew are then filled up with products such as stainless steel or titanium, which are preferred for their toughness and biocompatibility.
One more crucial technical development is using automated assembly lines. Automation in the assembly process ensures that derma rollers are generated at a high volume without compromising top quality. Automated systems can precisely place and attach microneedles to the roller, reducing the chance of human error and raising total effectiveness.
The assimilation of quality control technologies such as high-resolution imaging and optical scanners permits real-time evaluation of microneedles throughout the production procedure. These tools can discover problems or discrepancies from the preferred specs, making sure that only top-notch products reach the marketplace.
Innovation | Role in Microneedle Construction |
---|---|
Computer-Aided Layout (CAD) | Enables accurate preparation and modeling of microneedle structures. |
Laser Cutting | Makes sure consistent shapes and sizes are made with high precision. |
Micro-Molding | Creates specific molds for regular microneedle manufacturing. |
Automated Production Line | increases manufacturing quantity and consistency. |
High-quality Quality technologies | Provides real-time evaluation to preserve high item top quality. |
Common Challenges in Manufacturing Microneedles On A Derma Roller
The procedure of producing microneedles for derma rollers includes numerous intricate actions, each offering its own set of challenges. One of the key problems depends on achieving the precision required to create microneedles that are both efficient and secure for use. These microneedles need to be evenly sharp and of consistent length to guarantee they can permeate the skin uniformly without causing unnecessary damages or pain.
Another substantial obstacle is the selection and handling of products. The microneedles must be made from materials that are not only biocompatible but also resilient enough to endure duplicate usage. Metals like stainless steel and titanium are commonly used, yet ensuring their quality and pureness is important. Any kind of impurities or inconsistencies in the product can endanger the honesty of the microneedles, leading to potential wellness dangers for users.
The design procedure itself is additionally stuffed with problems. Creating microneedles that are sufficiently tiny and sharp while preserving structural stability requires advanced design techniques. The production procedure typically entails microfabrication using modern technologies such as laser cutting or etching, which have to be specifically regulated to achieve the desired specifications. Any kind of deviation, however minor, can lead to malfunctioning products.
Sterilization is one more critical facet that offers its own set of obstacles. Microneedles have to be completely decontaminated to stop infection when utilized on the skin. Nevertheless, the sanitation process needs to be carefully taken care of to avoid harming the microneedles or jeopardizing their efficiency. Strategies such as gamma irradiation or ethylene oxide gas are commonly used, yet each method calls for careful calibration and tracking.
Making certain quality assurance throughout the production process is additionally a significant obstacle. Each microneedle must be checked for issues, which calls for sophisticated imaging and measurement technologies. Automated systems are often employed, but human oversight is still needed to capture any kind of anomalies that makers may miss out on. Maintaining a high standard of quality assurance is vital to generating trusted and efficient derma rollers.
Finally, ecological considerations can not be forgotten. The manufacturing procedure should be made to minimize waste and lower the ecological impact. This includes not only the materials utilized, but also the energy consumption and emissions connected with manufacturing. Locating lasting solutions while preserving product quality and effectiveness is a continuous challenge in the industry.
Environmental Considerations in Microneedle Production
In the production of microneedles for derma rollers, interest to ecological effect is important. The procedure entails a number of phases, each of which can have significant ramifications for sustainability and ecological impact. There are numerous essential locations where environmental factors to consider come into play.
Material Option
One of the primary factors is the selection of products. The microneedles are normally made from metals like stainless-steel or titanium, but progressively, there is a shift in the direction of naturally degradable and biocompatible polymers. These products not only minimize environmental worry but also make sure that the items are safer for individuals.
Production Processes
Production approaches, such as laser cutting and precision molding, need to be maximized to reduce waste. For instance, the accuracy of the design of microneedles commonly involves advanced modern technologies that can precisely control material usage, thereby lowering excess waste. Furthermore, reusing and repurposing scrap products from these processes can further boost sustainability.
Energy Consumption
One more major consideration is the energy intake associated with the production procedure. Production facilities are required to execute energy-efficient techniques and equipment to lower their carbon footprint. Using renewable resource resources, such as solar or wind power, can additionally contribute substantially to making the production procedure extra lasting.
Packaging and Transport
The packaging of derma rollers and their microneedles also plays a role in ecological effect. Utilizing recyclable or naturally degradable packaging products helps reduce waste. In addition, optimizing transport logistics to decrease carbon emissions via efficient direction and the use of environmentally friendly vehicles is important.
Waste Administration
Efficient waste management techniques are important in microneedle production. This consists of appropriate disposal of harmful products, recycling programs for production waste, and the application of zero-waste plans. Firms have to guarantee that they follow ecological policies and continually look for means to lower their waste outcome.
Factors to Consider | Effect | Reduction Strategies |
---|---|---|
Product Selection | Environmental problems of raw materials | Use naturally degradable and biocompatible products |
Production Processes | Waste generation | Enhance precision engineering, reuse scrap |
Power Intake | Carbon impact | Implement energy-efficient practices, use renewable resource |
Product packaging and Transportation | Waste and emissions | Use environment-friendly packaging, enhance logistics |
Waste Management | Pollution and disposal problems | Reusing programs, conformity with laws |
By concentrating on these ecological considerations, the microneedle production industry can dramatically lower its eco-friendly impact while continuing to offer top-quality items for consumers. Sustainability in this market not only benefits the environment but also aligns with growing customer need for green items.
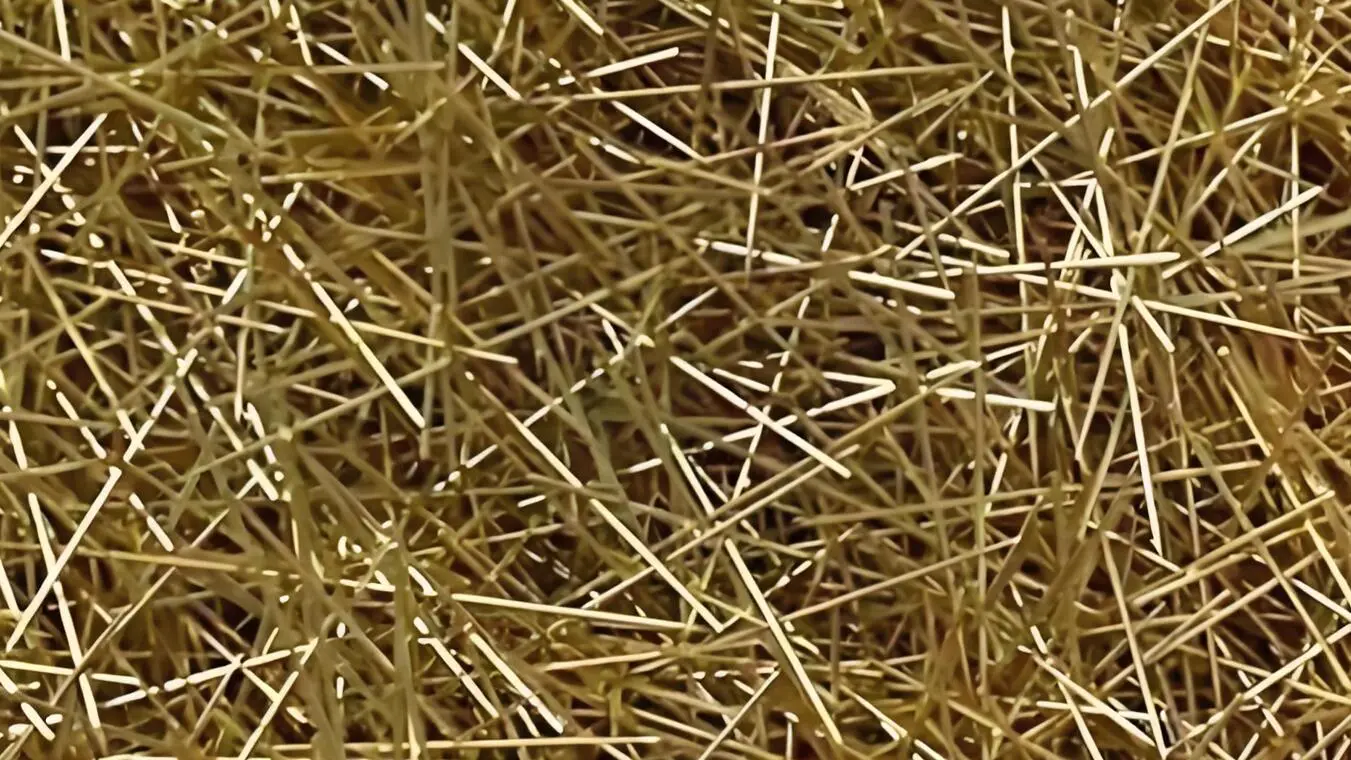
Future Trends in Derma Roller Microneedle Manufacturing
As we look ahead, several emerging patterns are set to reinvent the manufacturing of microneedles for derma rollers. These improvements are driven by the need for greater precision, boosted security, and enhanced individual end results.
1. Advanced Products
One considerable pattern is the growth and usage of sophisticated materials. Future microneedles may be made from biocompatible polymers and nanocomposites, which offer higher stamina, flexibility, and reduced danger of sensitive responses. These materials additionally enable the integration of medicine distribution systems straight into the microneedles, broadening the therapeutic applications of derma rollers.
2. Microfabrication Techniques
Developments in microfabrication technology, such as 3D printing and laser cutting, are poised to enhance the precision and effectiveness of microneedle production. These techniques allow for the development of intricate needle geometries that can improve skin infiltration and lower discomfort throughout usage. Additionally, they enable rapid prototyping and customization, satisfying individual needs.
3. Automation and AI Combination
The consolidation of automation and fabricated intelligence (AI) right into the manufacturing process will streamline manufacturing and ensure regular, high quality. AI algorithms can keep an eye on and readjust criteria in real-time, reducing flaws and increasing yield. Automated systems can likewise manage the elaborate set-up and packaging procedures, boosting performance even more.
4. Enhanced Sterilization Methods
Future improvements in sanitation methods will ensure the highest degree of security and efficacy. Strategies such as electron light beam and plasma sanitation offer efficient microbial control without compromising the stability of the microneedles. These approaches are faster and more eco-friendly than typical sterilization strategies.
5. Sustainable Production Practices
Ecological considerations are becoming increasingly important in manufacturing. Future patterns will likely concentrate on lasting techniques, such as utilizing recycled products and eco-friendly product packaging. Furthermore, suppliers will aim to lower waste and energy consumption throughout the manufacturing procedure, aligning with global sustainability goals.
Trend | Description | Effect |
---|---|---|
Advanced Products | Use of biocompatible polymers and nanocomposites | Better strength, flexibility, and reduced allergies |
Microfabrication Techniques | 3D printing and laser cutting | Improved accuracy, effectiveness, and customization |
Automation and AI Integration | Real-time tracking and adjustments | Consistent quality and boosted return |
Enhanced Sanitation Techniques | Electron beams of light and plasma sanitation | Reliable microbial control and ecological advantages |
Sustainable Production Practices | Use of recycled materials and environment-friendly packaging | Minimized waste and power usage |
Finally, the future of microneedle production for derma rollers is bright, with various improvements established to enhance the safety, security, efficiency, and ecological sustainability of the manufacturing process. These patterns will certainly not just improve the customer experience but additionally expand the therapeutic potential of derma rollers in clinical and cosmetic applications.
FAQs about Derma Roller Microneedles
What materials are used in manufacturing microneedles for derma rollers?
The materials commonly used for microneedles on derma rollers include medical-grade stainless steel, titanium, polymers, silicon, and ceramics. These materials are chosen for their biocompatibility, strength, and manufacturing feasibility.
How are microneedles on derma rollers manufactured?
The manufacturing process of microneedles involves precision engineering techniques such as micro-molding, laser cutting, and electrochemical etching. These methods ensure that each microneedle is produced to exact specifications, providing consistency in performance and safety.
What are the challenges in manufacturing microneedles for derma rollers?
Some common challenges in microneedle manufacturing include achieving precision in production, selecting and handling materials, designing microneedles with complex geometries, ensuring effective sterilization, maintaining quality control, and addressing environmental considerations.
What are the future trends in derma roller microneedle manufacturing?
Future trends in microneedle manufacturing include the use of advanced materials like biocompatible polymers, advancements in microfabrication techniques such as 3D printing, integration of automation and AI for efficiency, enhanced sterilization methods, and a focus on sustainable manufacturing practices to reduce environmental impact.