Table of Contents
ToggleThe Role of Logistics in Derma Roller Distribution
In the dynamic world of skincare, understanding the role of logistics in derma roller distribution is crucial for success. This article delves into the intricate components of logistics, from supply chain design to transportation planning, highlighting how each element contributes to efficiency and customer satisfaction. By optimizing these processes, businesses can ensure timely delivery, maintain product integrity, and ultimately enhance consumer trust in their brand.
Furthermore, we explore innovative strategies and technologies that streamline operations, such as real-time tracking and advanced inventory management systems. By leveraging these tools, companies can navigate the challenges of supply chain management while preventing stockouts and overstocks. Join us as we uncover the secrets to mastering the role of logistics in derma roller distribution and achieving operational excellence in this competitive market.
Components of Logistics in Derma Roller Distribution
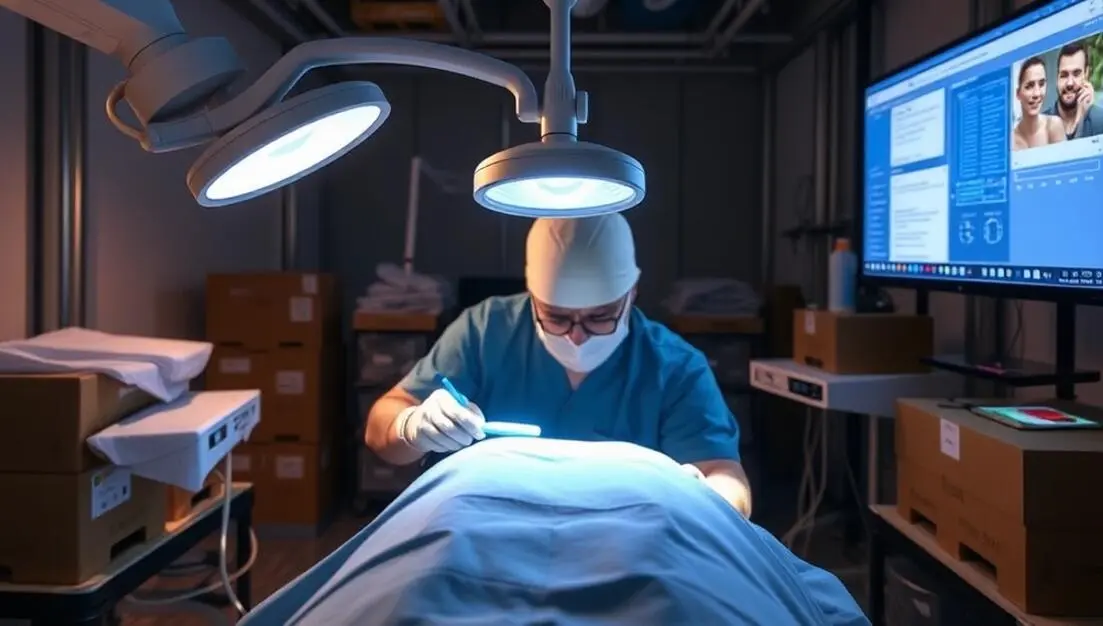
1. Supply Chain Design
The logistics in derma roller distribution begins with an effective supply chain design. This entails determining trusted suppliers for raw products and elements, collaborating manufacturing routines, and ensuring smooth assimilation between procurement, production, and distribution. A robust supply chain style reduces preparations, reduces prices, and improves item schedule out there.
2. Supply Management
Reliable supply management is vital to stop overstocking and stockouts. For derma roller distribution, preserving an optimal inventory degree is necessary as a result of the accuracy and top quality requirements of these items. Methods such as Just-in-Time (JIT) supply, need projecting, and automated inventory tracking make certain real-time exposure into stock degrees and reduce wastage.
3. Warehousing and Storage
Proper warehousing techniques are crucial for preserving the quality of derma rollers. Given their delicate needles and packaging, these products require controlled environments to prevent damage. Key considerations for warehousing include:
Aspect | Demand |
---|---|
Storage Conditions | Temperature-controlled, dust-free, and completely dry settings. |
Organization | Effective shelving systems to stop physical damage and simplify order picking. |
Security | Enhanced measures to avoid theft or unauthorized access. |
4. Product packaging and Handling
Packaging is an essential element in the logistics in derma roller distribution. Correct derma roller packaging ensures the items continue to be sterilized and intact throughout the supply chain. Key elements include using tamper-proof and eco-friendly products, compliance with regulative requirements, and ergonomic styles for very easy handling and transportation.
5. Transport Planning
Reliable transportation options are crucial to guarantee timely delivery of derma rollers to circulation centers, stores, and finish customers. This involves choosing the best mix of transportation settings (air, sea, or land), maximizing routes to decrease transit times, and monitoring automobile problems to maintain product integrity.
6. Technology Integration
Modern technology plays an important role in optimizing logistics in derma roller distribution. Tools such as Warehouse Management Systems (WMS), Transportation Management Systems (TMS), and real-time tracking software program enhance operational effectiveness, boost decision-making, and make sure end-to-end presence throughout the supply chain.
Supply Chain Optimization for Efficient Product Delivery
Effective supply chain monitoring plays a critical role in ensuring the seamless circulation of derma rollers. By maximizing each element of the supply chain, services can reduce prices, improve distribution speed, and improve total client fulfillment. Below, we explore the vital areas where supply chain optimization drives success in logistics for derma roller distribution.
Demand Forecasting and Planning
Accurate derma roller demand forecasting is essential for optimizing the supply chain. By analyzing historical sales data, market trends, and seasonal fluctuations, businesses can effectively predict inventory needs. This helps ensure the availability of derma rollers while avoiding challenges such as stockouts or overstocking, which can disrupt the logistics process.
Provider Coordination
Maintaining strong control over distributors is crucial for ensuring a steady flow of resources and finished products. Building long-term partnerships with reliable suppliers ensures timely procurement and reduces the risk of supply chain disruptions. For derma roller distribution, upholding high standards at the supplier level is equally important to meet customer expectations.
Central vs. Decentralized Distribution
Picking the best distribution design dramatically impacts efficiency. A central distribution system can simplify operations by settling stock in a solitary location, reducing expenses. However, for larger geographical reach, a decentralized system with several stockrooms might be much more reliable for reducing delivery times in derma roller logistics.
Data-Driven Decision Making
Leveraging technology and analytics tools is key to optimizing supply chains. Real-time tracking of inventory levels, supplier performance, and shipping metrics enables businesses to make data-driven decisions. These insights help identify bottlenecks and enhance overall logistics efficiency in derma roller distribution.
Derma Roller Lead Time Reduction
Reducing lead time for derma rollers is a key objective in supply chain optimization. This involves streamlining processes like order processing, product packaging, and transportation. Shorter lead times allow companies to respond quickly to market demands and offer customers an exceptional delivery experience.
Expense Management Strategies
Cost effectiveness is a core component of an enhanced supply chain. Companies can achieve this by bargaining positive terms with suppliers, settling shipments, and employing course optimization strategies. For derma roller distribution, balancing price control with maintaining product high quality is a critical factor to consider.
Combination of Logistics Partners
Working together with dependable third-party logistics (3PL) providers improves supply chain capacities. These companions bring specialized knowledge in transport, warehousing, and personalizeds clearance for worldwide distributions, making certain smooth logistics operations in derma roller distribution.
Storage Facility Management Strategies for Derma Roller Stocking
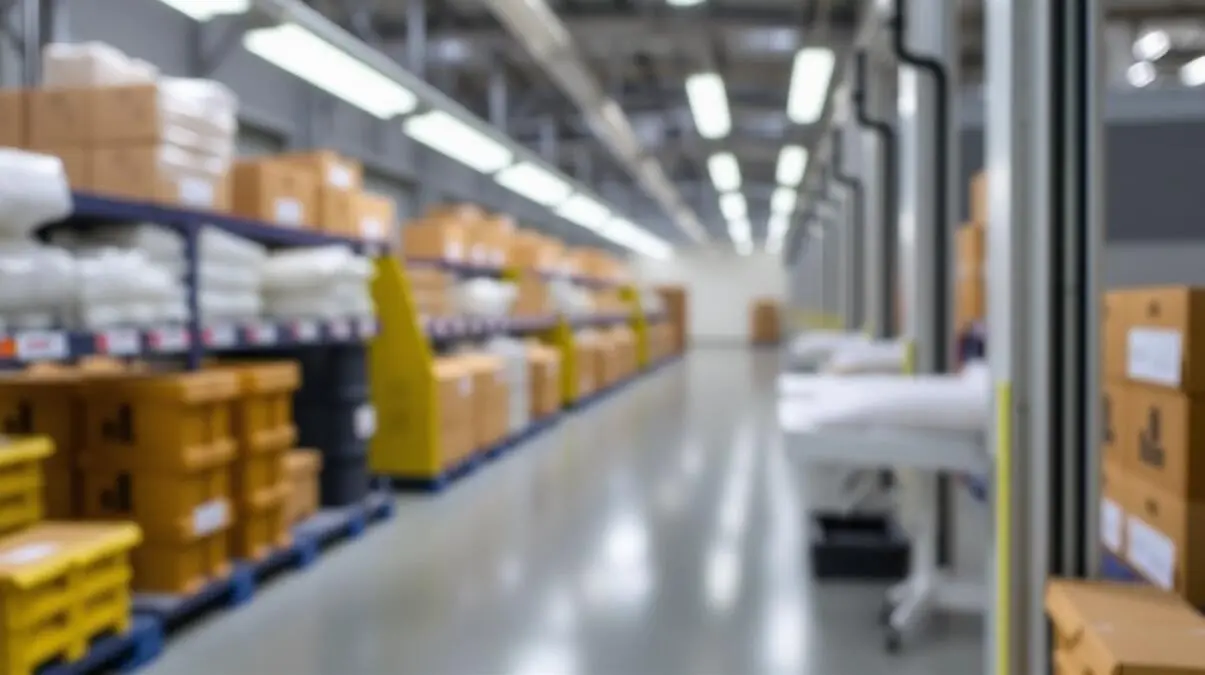
Importance of Efficient Warehouse Management
Reliable storage facility management is crucial for ensuring smooth logistics in derma roller distribution. Proper inventory management helps maintain a steady flow of stock, minimize delays, and meet customer demands efficiently. By organizing storage and implementing streamlined procedures, warehouses can significantly reduce operational costs and improve delivery timelines.
Maximized Storage Layout for Derma Rollers
A strategic storage design is essential for handling derma rollers, which are compact yet require careful management due to their delicate packaging. Storage facilities should implement a zoned design system, which includes:
Zone Type | Purpose |
---|---|
Obtaining Zone | For checking and sorting incoming supply. |
Storage space Zone | For organized equipping based upon SKU (Stock Keeping Unit). |
Selecting Zone | For quick accessibility to products for order satisfaction. |
Loading Zone | For securely packaging derma rollers for delivery. |
Temperature and Humidity Control
Given that derma rollers are sensitive to ecological elements, maintaining appropriate temperature and moisture levels in the warehouse is necessary to protect against damage. Storehouses must be furnished with monitoring systems to guarantee regular conditions. This is especially crucial for protecting item quality throughout long-term storage.
Supply Management Systems (IMS)
Implementing advanced Inventory Management Systems (IMS) is a keystone of effective logistics in derma roller distribution. These systems enable real-time monitoring of supply levels, automated restocking notifies, and precise need projecting. Key functionalities include:
Feature | Benefit |
---|---|
Real-Time Tracking | Provides visibility into present supply degrees. |
Restocking Alerts | Prevents stockouts by alerting when supply is low. |
Demand Forecasting | Makes certain optimal supply degrees based on sales patterns. |
Safety And Security and Handling Protocols
Derma rollers are packaged in portable yet breakable containers, requiring strict safety and security and handling protocols. Staff training is essential to guarantee correct handling during equipping and access. Additionally, storehouses should make use of shelving systems made to stop physical damages, such as supported racks and anti-tip mechanisms.
Periodic Stock Audits
Normal supply audits are vital for keeping exact stock records and identifying disparities. This procedure helps improve efficiency in logistics in derma roller distribution by decreasing errors, enhancing supply rotation, and making sure that older stock is delivered initially to prevent expiry or damage.
Role of Technology in Streamlining Derma Roller Logistics
Enhancing Visibility Through Real-Time Tracking
One of the most transformative innovations in logistics in derma roller distribution is making use of real-time radar. These innovations give end-to-end presence of shipments, enabling stakeholders to keep an eye on the condition and area of derma roller consignments at any given moment. This level of transparency not only guarantees prompt shipments but also assists mitigate dangers such as hold-ups or misplacement of products.
Assimilation of Warehouse Management Systems (WMS)
Modern storage facility administration systems (WMS) are crucial in enhancing the storage and handling of derma rollers. These systems utilize data analytics and automation to streamline stock company, improve selecting and packing efficiency, and minimize human mistake. By integrating WMS, firms can considerably improve their capability to meet consumer demands while maintaining price efficiency.
Automation in Order Processing
Automation modern technologies, such as robotic selecting systems and automated sorters, play a critical role in accelerating the order gratification process. This is specifically essential in the distribution of derma rollers, where prompt delivery is a vital variable in client satisfaction. Automated options reduce processing times and make certain that deliveries are ready properly and efficiently.
Advanced Transportation Management Systems (TMS)
Transportation monitoring systems (TMS) have actually changed the planning and implementation of shipment courses. These systems maximize transportation paths based on factors like range, website traffic patterns, and distribution time home windows. Foracross the country and global derma roller distribution, TMS makes sure economical and timely transport while reducing environmental influence via course optimization.
Anticipating Analytics for Demand Forecasting
Anticipating analytics devices utilize historical sales information and market trends to anticipate future need for derma rollers. By leveraging these insights, services can make educated decisions regarding stock levels, minimizing the risk of both stockouts and overstocks. This positive method straightens stock control with consumer need, guaranteeing a smooth distribution process.
Blockchain for Supply Chain Transparency
Blockchain innovation is becoming a powerful tool for enhancing openness and protection in the supply chain. By producing an unalterable journal of deals, blockchain makes certain that every step in the logistics of derma roller distribution can be confirmed and mapped. This innovation cultivates count on amongst stakeholders and enhances total supply chain accountability.
Mobile Applications for Last-Mile Delivery
Mobile applications have become essential for managing last-mile delivery operations. These apps provide real-time updates to delivery personnel and customers, ensuring smooth communication and timely shipments. For businesses involved in derma roller distribution, mobile technology enhances customer satisfaction by offering accurate delivery timelines and resolving issues quickly.
Stock Control Techniques to stop Stockouts and Overstocks
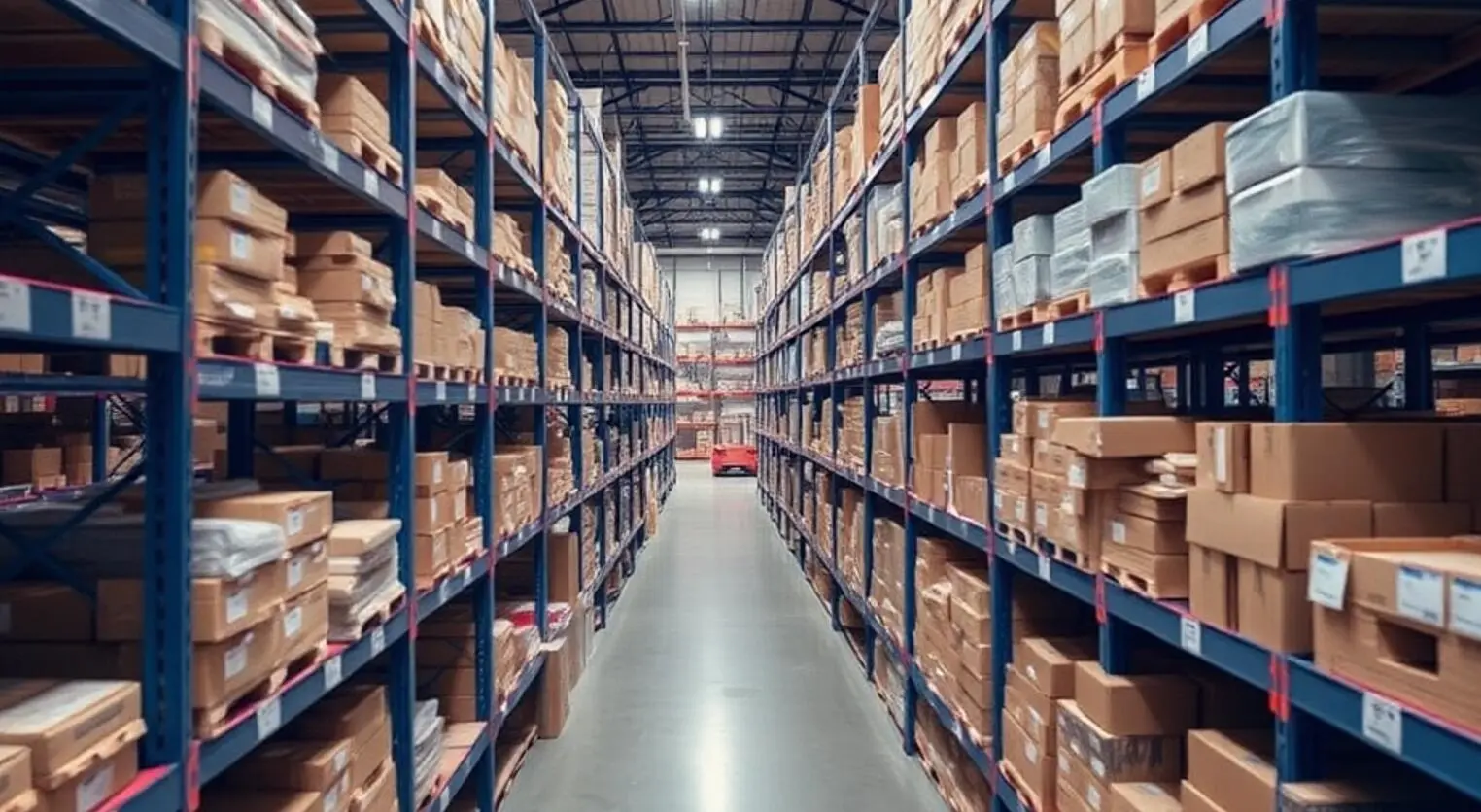
Value of Inventory Control in Logistics
Efficient supply control is essential for maintaining the balance between supply and need in logistics in derma roller distribution. A well-optimized supply system makes sure enough stock levels to meet client needs while lessening excess supply that ties up resources.
Demand Forecasting and Planning
Precise demand projecting is the foundation of efficient supply control. Utilizing historic sales information, seasonal trends, and market analysis allows the development of robust demand forecasts. Tools such as predictive analytics and AI-driven projecting software application can enhance accuracy and reduce unpredictabilities.
Data Source | Purpose | Final result |
---|---|---|
Historical Sales Data | Examine previous efficiency | Determine trends |
Market Analysis | Understand existing demand | Change equipping degrees |
Seasonal Trends | Prepare for changes | Get ready for peak need |
Embracing an Inventory Management System
Implementing an inventory tracking system is essential for real-time monitoring of derma roller stock levels. Features like barcode scanning, RFID tracking, and cloud-based platforms allow seamless integration with supply chain operations. These systems enhance visibility and help prevent errors that could result in stockouts or overstocking.
Setting Reorder Points and Safety Stock Levels
Identifying appropriate reorder points and safety and security stock degrees is crucial for ensuring continual availability of derma rollers. These specifications are computed based on preparations, need variability, and solution level goals. Frequently reviewing and upgrading these values boosts responsiveness to transforming market problems.
Specification | Function | Effect |
---|---|---|
Reorder Points | Trigger replenishment | Avoid stockouts |
Safety Stock | Barrier versus irregularity | Guarantee constant supply |
Decreasing Inventory Holding Costs
Overstocking increases holding prices, that include storage, insurance coverage, and devaluation. To address this, periodic stock reviews and optimization methods like Just-In-Time (JIT) replenishment can be utilized. These approaches enhance stocking methods while keeping item accessibility.
Cycle Counting and Inventory Audits
Performing regular cycle counts and inventory audits ensures the accuracy of inventory records. By resolving disparities in between physical supply and system information, these processes boost dependability and support notified decision-making in derma roller distribution logistics.
Collaboration with Supply Chain Partners
Close collaboration with providers and distributors plays an essential role in taking care of stock. Sharing real-time information and need projections with companions makes it possible for synchronized replenishment, decreasing the risk of both stockouts and overstocks.
Packaging and Handling Requirements for Derma Roller Distribution
Value of Proper Packaging in Logistics
Reliable logistics in derma roller distribution rest on making use of durable packaging that makes certain item integrity during transportation. Derma rollers, being accuracy skincare tools, need product packaging that safeguards against physical damage, contamination, and environmental aspects such as moisture and temperature level variations. This is particularly critical when delivering throughout regions with varying environments or throughout long-distance transport.
Material Selection for Packaging
Premium materials such as corrugated boxes, foam inserts, and tamper-evident seals should be utilized. These products safeguard the item and share a feeling of professionalism and reliability and treatment to the customer. For derma rollers, added sterile barriers such as diminish wraps or private blister packs are necessary to preserve health and conformity with wellness regulations.
Classifying and Regulatory Compliance
Clear and precise labeling is an essential facet of logistics in derma roller distribution. Labels should include item information, handling instructions, and regulatory info such as set numbers and expiration days. For global shipments, compliance with customizeds and wellness authority demands ensures smooth transportation and stays clear of delays or fines.
Taking Care Of Procedures to Ensure Product Safety
Cautious handling techniques are required to stop damages to derma rollers throughout numerous stages of the supply chain. Personnel training programs ought to emphasize gentle handling and the proper piling of packaged items to avoid pressure-related contortion. Additionally, implementing typical operating procedures (SOPs) for getting, storage, and dispatch minimizes the risk of mishandling.
Product Packaging Design for Brand Identity and Customer Experience
Past useful requirements, product packaging needs to align with the brand name’s identity. Eye-catching styles and green products can boost consumer fulfillment and reinforce brand name commitment. Product packaging made for very easy unboxing additional boosts the end-user experience while making sure the item remains safe and secure till it reaches the customer.
Technological Solutions for Packaging and Handling
Automation in packaging processes, such as automated sealing and identifying systems, simplifies operations and decreases mistakes. Real-time surveillance remedies, such as RFID tags or QR codes, can be incorporated into the packaging to track derma rollers throughout the supply chain. These modern technologies offer transparency, boost functional effectiveness, and strengthen count on logistics in derma roller distribution.
Transport Solutions for Nationwide and Global Delivery
Significance of Transportation in Logistics for Derma Roller Distribution
Transport is an essential element of logistics in derma roller distribution, ensuring timely delivery to domestic and international markets. Effective transport systems reduce hold-ups, decrease prices, and keep item integrity throughout transit. Whether supplying to local derma roller retailers or delivery worldwide, calculated transportation planning is crucial for operational success.
Domestic Transportation Strategies
For across the country distribution, leveraging a combination of road, rail, and air transport makes sure adaptability and cost-efficiency. Picking proper transport modes relies on elements such as distribution timelines, range, and local facilities. Implementing a hub-and-spoke version can enhance courses by consolidating deliveries at central centers before distributing them to local storage facilities or retail areas.
Methods for efficient domestic transport consist of:
Practice | Advantage |
---|---|
Optimized directing | Reduces fuel expenses and shipment times |
Partnerships with local providers | Boosts last-mile distribution efficiency |
Real-time shipment monitoring | Boosts exposure and consumer interaction |
Worldwide Transportation Solutions
Worldwide delivery requires robust preparation to navigate cross-border guidelines, custom-mades processes, and varying market conditions. Air and sea freight are the main settings for worldwide shipments, chosen based on cost, urgency, and item quantity.
To guarantee smooth worldwide transport, business ought to concentrate on:
Solution | Summary |
---|---|
International freight collaborations | Working together with seasoned products forwarders for regulative compliance and customs clearance |
Multi-modal transport choices | Integrating air, sea, and rail transport for affordable solutions |
Innovation assimilation | Using transport management systems (TMS) for end-to-end shipment monitoring |
Making Sure Product Integrity During Transportation
Maintaining the quality of derma rollers throughout transit is a top priority. Proper packaging and taking care of protocols are critical to stop damage. In addition, transport conditions such as temperature and moisture control might be needed to shield the items.
Recommended steps consist of:
- Using protective product packaging materials to prevent physical damages.
- Applying climate-controlled transportation for sensitive products.
- Conducting routine audits of transportation carriers to guarantee conformity with high quality requirements.
Attending To Challenges in Transportation
Difficulties such as varying gas prices, hold-ups at personalizeds, and capacity restrictions can disrupt logistics in derma roller distribution. To alleviate these problems, firms ought to establish contingency plans, expand their service provider network, and buy predictive analytics to expect potential interruptions.
Monitoring and Improving Last-Mile Delivery for Customer Satisfaction
Significance of Last-Mile Delivery in Logistics for Derma Roller Distribution
The last of product shipment, referred to as last-mile distribution, is important for ensuring customer complete satisfaction. In the context of logistics in derma roller distribution, this phase bridges the gap between warehouses and finish consumers. Reliable last-mile delivery directly influences customer loyalty, brand name credibility, and market competition.
Obstacles in Last-Mile Delivery
Typical obstacles encountered throughout last-mile distribution consist of:
Challenge | Impact |
---|---|
Shipment Delays | Minimizes consumer satisfaction and depend on. |
High Costs | Boosts the total functional costs of the logistics system. |
Incorrect Deliveries | Causes product returns and added logistical inadequacies. |
Lack of Real-Time Visibility | Prevents proactive problem resolution and decreases functional transparency. |
Approaches for Enhancing Last-Mile Delivery Efficiency
To improve the efficiency of logistics in derma roller distribution, services can take on the adhering to techniques:
Strategy | Summary |
---|---|
Path Optimization | Leverage GPS and AI-based devices to reduce shipment times and gas costs. |
Real-Time Tracking | Offer customers and logistics groups with updates on distribution status. |
Local Warehousing | Usage local centers to lower transit time and prices for regional distributions. |
Versatile Delivery Options | Deal customers selections such as same-day shipment or arranged time slots. |
Automation and Drones | Implement autonomous vehicles and drones to boost delivery rate. |
Keeping Track Of Key Performance Indicators (KPIs)
Tracking and assessing crucial performance signs (KPIs) is crucial for gauging and boosting the performance of last-mile delivery. Essential KPIs for logistics in derma roller distribution consist of:
KPI | Importance |
---|---|
On-Time Delivery Rate | Shows dependability and preparation of distributions. |
Shipment Cost per Order | Helps display and optimize costs. |
Customer Feedback Score | Measures fulfillment with delivery services. |
Return and Replacement Rate | Shows issues connected to incorrect or broken shipments. |
Leveraging Technology for Continuous Improvement
Innovation plays a pivotal role in enhancing last-mile delivery for derma roller circulation. Businesses can purchase innovative logistics monitoring systems, real-time monitoring tools, and predictive analytics to determine locations for renovation and proactively address delivery concerns. Additionally, automation innovations, such as drones and independent delivery vehicles, can lower reliance on hands-on labor while enhancing speed and precision.
Customer-Centric Approach to Last-Mile Delivery
Embracing a customer-centric strategy ensures that last-mile distribution lines up with customer assumptions. Personalized distribution alternatives, proactive interaction regarding hold-ups, and easy to use return procedures can significantly enhance client fulfillment. By concentrating on the needs of completion consumer, organizations can construct lasting partnerships and establish an affordable side in the logistics of derma roller distribution.
Verdict
Effective tracking and constant improvement of last-mile distribution processes are important for attaining high levels of consumer fulfillment. By resolving difficulties, executing critical services, and leveraging modern technology, businesses can optimize their logistics operations for derma roller distribution and satisfy the needs of contemporary consumers with effectiveness and reliability.
FAQs about Logistics in Derma Roller Distribution
1. What is the importance of logistics in derma roller distribution?
Logistics plays a vital role in derma roller distribution by ensuring products are transported efficiently from microneedle derma roller manufacturers to end-users. It involves managing inventory, selecting optimal transportation methods, and ensuring timely deliveries. Effective logistics can reduce costs, improve customer satisfaction, and maintain product quality during transit.
2. How can logistics in derma roller distribution affect delivery time?
Logistics in derma roller distribution directly impacts delivery time. By streamlining supply chain processes, utilizing local warehouses, and partnering with reliable courier services, logistics can help minimize delays and ensure faster deliveries to customers. Real-time tracking systems and efficient route planning also contribute to quicker delivery.
3. What are the key logistical challenges in derma roller distribution?
Key logistical challenges in derma roller distribution include ensuring safe and secure transportation, managing customs for international shipments, maintaining product quality during transit, and dealing with fluctuating demand. Additionally, coordinating with multiple distributors, maintaining proper inventory levels, and adhering to regulations are critical aspects.
4. How does inventory management fit into logistics for derma roller distribution?
Inventory management is a key component of logistics in derma roller distribution. It ensures that the correct quantity of derma rollers is available for shipment when needed. Efficient inventory management minimizes stockouts, reduces excess stock, and helps distributors meet demand accurately while maintaining cost efficiency.
5. What transportation options are involved in logistics for derma roller distribution?
Logistics in derma roller distribution can involve a variety of transportation methods, depending on the size of the order, delivery speed, and destination. Common options include road transportation (for local deliveries), air freight (for faster international deliveries), and sea freight (for larger shipments at a lower cost). Each method has its pros and cons regarding cost and delivery speed.
6. How does packaging influence logistics in derma roller distribution?
Packaging is a crucial part of logistics in derma roller distribution as it protects the product during transportation and handling. Proper packaging helps prevent damage, contamination, and ensures that the derma rollers are delivered in optimal condition. It also ensures compliance with legal and regulatory requirements, especially for medical devices or cosmetic products.
7. How can logistics optimize cost in derma roller distribution?
Logistics can optimize costs in derma roller distribution by selecting the most efficient transportation routes, minimizing delays, reducing storage fees through better inventory management, and consolidating shipments when possible. Efficient supply chain planning and using automation tools can also help lower labor costs and reduce wastage.
8. What role does technology play in logistics for derma roller distribution?
Technology plays a major role in optimizing logistics in derma roller distribution. Inventory management software, real-time tracking systems, and automated warehouse solutions enable distributors to monitor and control stock levels, streamline order fulfillment, and track shipments. These technologies improve efficiency, reduce errors, and enhance customer satisfaction.
9. How do customs regulations affect logistics in derma roller distribution?
Customs regulations are an important consideration in logistics for international derma roller distribution. Products must meet specific import/export requirements, such as safety certifications and product documentation. Failure to comply with these regulations can result in delays, fines, or shipments being returned, impacting the efficiency of the logistics process.
10. How can logistics companies improve customer satisfaction in derma roller distribution?
Logistics companies can improve customer satisfaction in derma roller distribution by ensuring timely deliveries, offering accurate tracking information, and providing responsive customer service for any shipping-related concerns. By maintaining high standards of packaging and product handling, logistics companies also ensure that customers receive undamaged and compliant products.
References
- Logistics Management, “The Role of Logistics in Healthcare Supply Chains,” https://www.logisticsmgmt.com/article/the_role_of_logistics_in_healthcare_supply_chains
- Supply Chain 24/7, “How Logistics Can Improve Customer Satisfaction,” https://www.supplychain247.com/article/how_logistics_can_improve_customer_satisfaction
- Inbound Logistics, “The Importance of Efficient Logistics in Distribution,” https://www.inboundlogistics.com/cms/article/the-importance-of-efficient-logistics-in-distribution/
- Business.com, “How to Choose the Right Logistics Partner,” https://www.business.com/articles/how-to-choose-the-right-logistics-partner/
- ScienceDirect, “Logistics in the Pharmaceutical and Medical Device Industry,” https://www.sciencedirect.com/science/article/pii/S1877056911001396
- SupplyChainDigital, “Logistics Challenges in the Cosmetic and Medical Device Industry,” https://www.supplychaindigital.com/logistics/logistics-challenges-in-the-cosmetic-and-medical-device-industry
- Logistics Viewpoints, “How to Optimize Logistics Costs,” https://logisticsviewpoints.com/2020/02/24/how-to-optimize-logistics-costs/
- Material Handling & Logistics, “The Role of Packaging in Logistics,” https://www.mhlnews.com/transportation-distribution/article/20913479/the-role-of-packaging-in-logistics
- Shipping Solutions, “Global Logistics and Shipping for Cosmetics and Medical Devices,” https://www.shippingsolutions.com/blog/global-logistics-and-shipping-for-cosmetics-and-medical-devices
- Logistics Business, “Improving Efficiency in Logistics for Medical Device Distribution,” https://www.logisticsbusiness.com/improving-efficiency-in-logistics-for-medical-device-distribution/
- Global Trade Magazine, “Logistics and Inventory Management in the Beauty Industry,” https://www.globaltrademag.com/logistics-and-inventory-management-in-the-beauty-industry/
- Modern Healthcare, “Regulatory Challenges in Medical Device Logistics,” https://www.modernhealthcare.com/article/20210928/NEWS/309289998
- Supply Chain Quarterly, “Best Practices for Handling and Storing Medical Devices,” https://www.supplychainquarterly.com/articles/1014-best-practices-for-handling-and-storing-medical-devices
- Journal of Business Logistics, “Logistics Strategies in Healthcare Product Distribution,” https://onlinelibrary.wiley.com/doi/abs/10.1002/jbl.301
- Transport Topics, “The Impact of Transportation on Medical Device Supply Chains,” https://www.ttnews.com/articles/impact-transportation-medical-device-supply-chains
- Global Cosmetics News, “Logistics and Distribution in the Cosmetics Industry,” https://www.globalcosmeticsnews.com/logistics-and-distribution-in-the-cosmetics-industry/