Table of Contents
ToggleKey Challenges in Derma Roller Manufacturing
As an experienced expert from a derma roller company, I delve into the intricate world of derma roller production, highlighting the challenges in derma roller manufacturing. One of the key challenges is achieving precision in needle production, where any deviation can affect product performance and safety. Material selection also poses a significant challenge in derma roller manufacturing, requiring high-quality, medical-grade materials. Ensuring consistent quality control throughout the manufacturing process is essential. Additionally, manufacturers face the challenge of meeting regulatory compliance standards while adopting new technologies to improve efficiency and maintain the highest standards of safety and effectiveness.
Maintaining Sterilization Standards
This article examines key challenges in derma roller manufacturing, including maintaining strict sterilization standards and meeting regulatory compliance. Proper sterilization processes, like gamma or EO sterilization for derma rollers, are essential for safety while navigating complex regulations ensures product efficacy. Overcoming these challenges helps manufacturers produce derma rollers that meet consumer expectations, ensuring both safety and effectiveness in skin care applications.
Understanding The Challenges in Derma Roller Manufacturing Processes
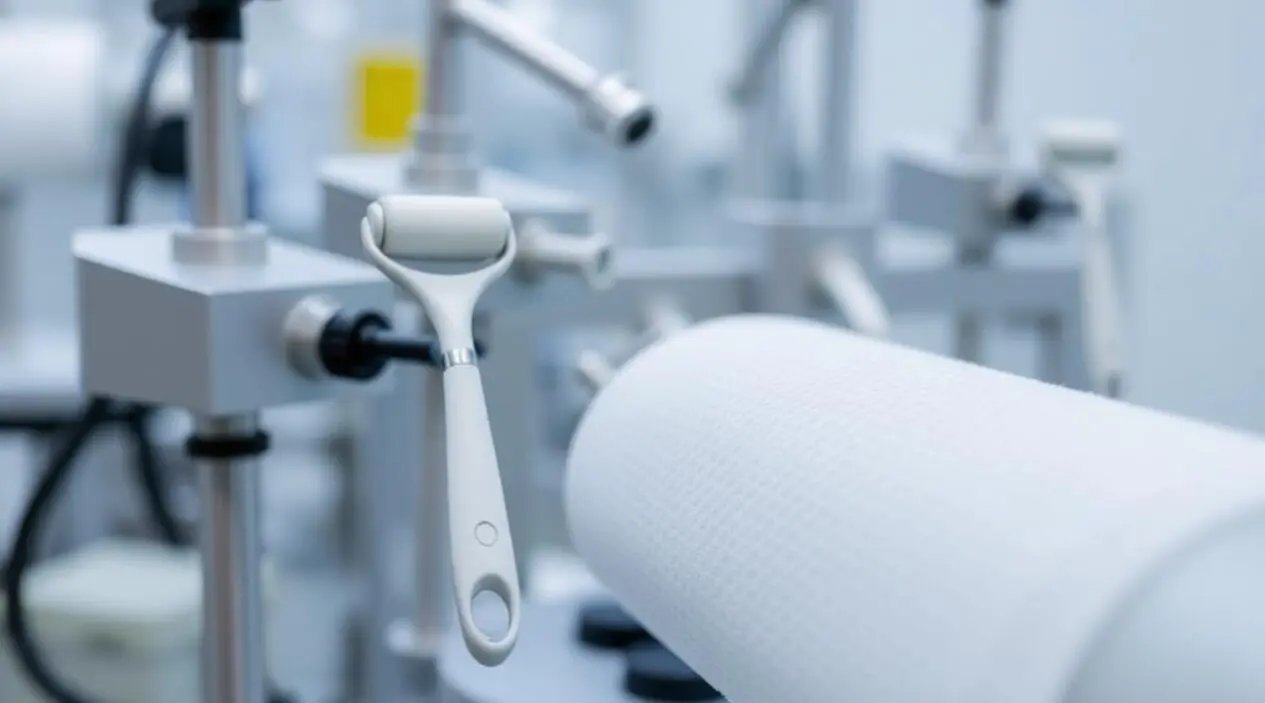
In my experience, the challenges in derma roller manufacturing start with a detailed understanding of the various procedures involved. Each step in the derma roller manufacturing process plays an essential role in ensuring the end product fulfills the highest possible standards of high quality and security.
Production Stages
The procedure commonly involves numerous crucial stages:
Stage | Description |
---|---|
Layout | Conceiving the derma roller’s specs, including needle size and setup. |
Material Selection | Selecting proper materials for the roller and needles, balancing cost and top quality. |
Needle Production | Manufacturing needles with precision to guarantee effectiveness and safety. |
Setting up | Integrating all components right into a natural, practical product. |
Sanitation | Executing strenuous sterilization procedures to maintain hygiene criteria. |
Product packaging | Designing product packaging that protects the item and connects its value. |
Key Considerations
One of the key challenges in derma roller manufacturing is preserving consistency across all these stages. Irregularity in any type of action can cause significant-high-quality concerns, which is why a robust quality management system is essential. Furthermore, the assimilation of innovations and developments can improve processes, and they also introduce complexity and require skilled personnel to handle them successfully.
In summary, understanding the elaborate procedures associated with derma roller manufacturing is important for conquering the integral challenges and ensuring the production of premium, secure, and efficient products.
Challenges in Derma Roller Manufacturing: Product Selection and Quality Control
In dealing with the challenges in derma roller manufacturing, one of the most important facets is the selection of ideal materials and making sure of rigorous high-quality control. The efficiency and safety of derma rollers greatly depend on the materials used in their construction. Consequently, makers must prioritize selecting materials that are long-lasting and safe for the skin to get in touch with.
Product Selection
The primary components of a derma roller are the deal with and the needles. The deal is generally made from medical-grade plastic or stainless steel, both of which should stand up to sanitation procedures and regular use. The needles, commonly crafted from surgical-grade stainless steel or titanium, need extraordinary sharpness and deterioration resistance. These products are chosen for their ability to maintain stability and performance over time.
Nevertheless, selecting the right products provides its own set of difficulties. Suppliers need to stabilize prices with top quality, making sure that the products meet both regulatory criteria and customer expectations. This includes considerable research study and screening to source materials that provide the very best mix of safety, resilience, and affordability.
Quality Assurance
Quality control is an additional significant factor to consider in derma roller manufacturing. Each part has to undergo extensive testing to guarantee it fulfills predefined standards. This includes evaluating the needles for uniformity and intensity, along with inspecting the takes for structural integrity. Quality assurance procedures typically involve both automated and hand-operated assessments to catch any kind of issues that could compromise the product’s safety, security, or efficiency.
Implementing a detailed quality assurance system can be challenging but is crucial to maintaining the trust of consumers and meeting regulatory requirements. Advanced technologies like computer-aided inspection and laser measurement are significantly being used to improve accuracy in high-quality evaluations.
Finally, the careful choice of materials and rigid quality assurance steps are foundational to conquering the obstacles in derma roller production. These efforts ensure that the final items are safe, effective, and dependable for end-users.
Challenges in Derma Roller Manufacturing: Accuracy in Needle Production

In the realm of derma roller manufacturing, attaining precision in needle manufacturing is a critical challenge that directly influences the efficiency, safety, and security of the final product. The process demands thorough attention to information and adherence to strict criteria to guarantee that each needle meets the called-for requirements.
Needle Material and Specifications
The selection of derma roller needle production is extremely important. Typically, stainless steel or titanium is used because of their strength and biocompatibility. The obstacle depends on guaranteeing that the product is without impurities and able to stand up to duplicated use without deterioration. Each needle should comply with specific measurements, typically measured in micrometers, to ensure harmony and performance.
Manufacturing Techniques
Advanced manufacturing methods such as laser cutting and micro-machining are used to create needles with the needed intensity and level of smoothness. These strategies should be carried out with high precision to maintain the structural integrity and functionality of the needles. The challenge is to continually produce needles that are sharp enough to permeate the skin without causing unnecessary trauma.
Quality Assurance and Testing
Quality control plays an essential role in needle production. Each batch of needles must undergo rigorous testing to verify their measurements, intensity, and longevity. This includes using high-resolution imaging and mechanical testing to guarantee that the needles satisfy the specified requirements. The challenge here is to keep a high degree of consistency throughout large manufacturing quantities.
Aspect | Challenge |
---|---|
Material Selection | Making certain pureness and longevity of materials like stainless steel or titanium. |
Production Techniques | Achieving specific sharpness and levels of smoothness making use of sophisticated techniques. |
Quality control | Maintaining consistency and conference specifications with rigorous screening. |
Dealing with these obstacles in derma roller manufacturing needs a combination of innovative innovation, proficient workmanship, and rigorous quality assurance measures. By getting rid of these obstacles, suppliers can generate derma rollers that are both effective and secure for customer usage.
Challenges in Derma Roller Manufacturing: Sterilization Standards and Practices
Among the considerable challenges in derma roller manufacturing revolves around ensuring stringent sanitation standards and techniques. Given the nature of derma rollers, which include direct contact with the skin, maintaining high degrees of sterility is extremely important to avoid infections and ensure individual safety and security.
Significance of Sterilization
Sanitation is vital in eliminating types of potential microbial contamination. This process shields the end-users and maintains the manufacturer’s track record. The complexity emerges from the requirement to stabilize efficient sterilization while maintaining the integrity and functionality of the derma roller’s elements.
Usual Sterilization Methods
Some methods are utilized in the market, including steam sanitation, ethylene oxide (EO) sanitation, and gamma radiation. Each approach has its own set of benefits and limitations. For circumstances, while heavy steam sterilization works, it might not be appropriate for all materials as a result of warm sensitivity. On the other hand, EO sanitation is gentle but needs mindful handling because of its poisonous nature.
Difficulties in Implementing Standards
Implementing these sterilization approaches regularly poses a challenge. Producers need to stick to strenuous protocols and continually monitor the process to ensure conformity with health and wellness and safety and security criteria. This involves investing in advanced tools and experienced workers, which can dramatically influence production prices.
Quality Control and Testing
Post-sterilization, derma rollers undergo comprehensive top-quality assurance screening to validate their sterility. This includes microbiological testing to identify any residual pollutants. The difficulty below hinges on maintaining an equilibrium between detailed testing and efficient production timelines.
Abiding By Global Standards
Makers should also browse the complexities of worldwide regulatory requirements, which can vary substantially throughout areas. Conformity with these regulations is vital for market accessibility and consumer trust. This typically requires a detailed understanding of various regulatory needs and the capacity to adapt processes appropriately.
To conclude, resolving the challenges in derma roller manufacturing related to sanitation includes a multifaceted approach, combining advanced technology, experienced knowledge, and stringent adherence to global requirements.
Challenges in Derma Roller Manufacturing: Regulatory Compliance and Certification
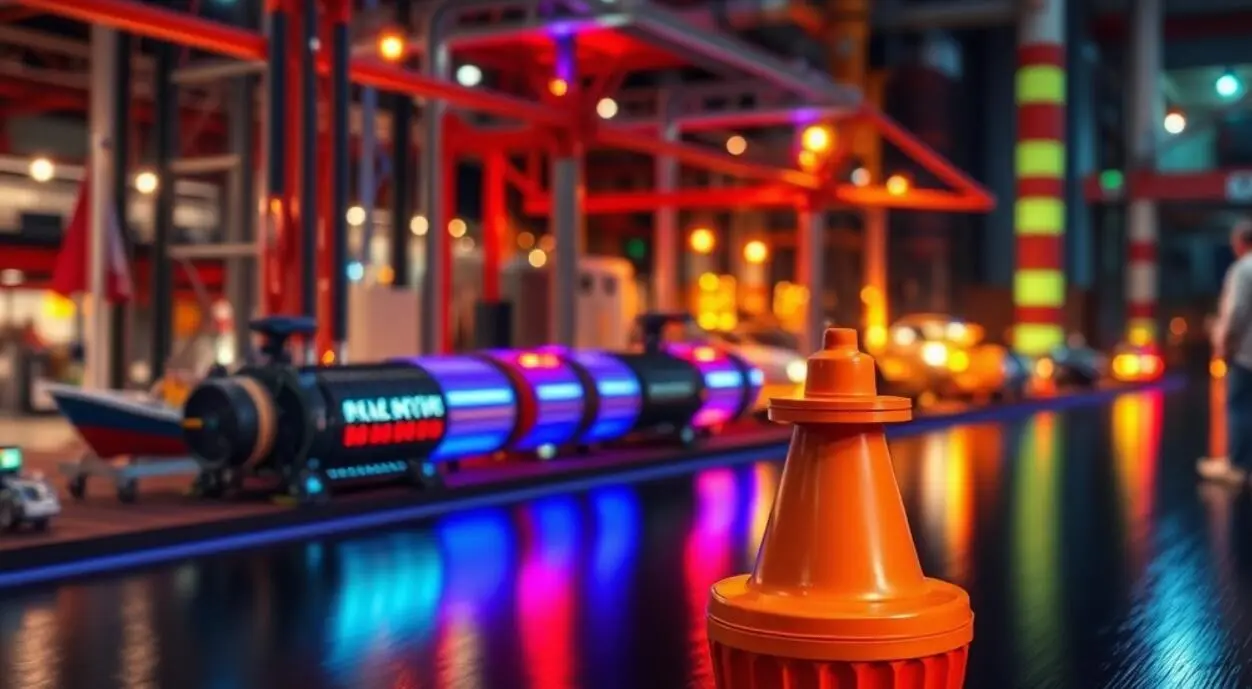
In the world of derma roller manufacturing, guaranteeing regulative conformity and obtaining essential certifications are crucial difficulties that makers deal with. The procedure involves adhering to strict guidelines established by different health and wellness authorities worldwide. These laws are designed to make sure that derma rollers are safe, effective, and of excellent quality.
Comprehending Regulatory Requirements
Manufacturers should have a deep understanding of the governing needs particular to the regions in which they plan to disperse their products. This includes conformity with criteria such as the FDA in the United States, the CE marking in the European Union, and other regional regulatory bodies. Each of these entities has its very own set of rules concerning the products used, the manufacturing procedure, and the completed product’s safety.
Accreditation Process
The accreditation process for derma rollers includes rigorous screening and documents. Makers need to offer proof that their products satisfy all safety, security, and efficacy standards. This frequently includes scientific trials, material safety data sheets, and in-depth item specifications. The procedure can be time-consuming and needs careful attention to information.
Obstacles in Maintaining Compliance
One of the main challenges in derma roller manufacturing is maintaining conformity with time. Rules can alter, and manufacturers should remain educated concerning any kind of updates to ensure continuous compliance. This needs a committed regulatory affairs team and a positive technique for keeping an eye on changes in regulations.
Paperwork and Record-Keeping
Appropriate paperwork and record-keeping are essential components of regulative compliance. Producers have to keep extensive records of their production processes, materials utilized, and quality assurance steps. This documentation is essential for audits and assessments by regulatory bodies.
Table of Key Regulatory Bodies and Their Requirements
Governing Body | Area | Trick Requirements |
---|---|---|
FDA | United States | Item registration, safety screening, identifying compliance |
CE Marking | European Union | Conformity evaluation, technical documentation, scientific evaluation |
TGA | Australia | Therapeutic Goods Administration approval, top quality administration system |
In conclusion, navigating the complex landscape of governing conformity and accreditation is a considerable difficulty in derma roller production. It requires a detailed understanding of international requirements and a dedication to keeping the highest degree of product safety and security and top quality.
Challenges in Derma Roller Manufacturing: Product Packaging and Safety Considerations
Value of Packaging in Derma Roller Manufacturing
In the realm of derma roller manufacturing, packaging plays a crucial role not only in protecting product honesty but also in ensuring customer safety and security. The packaging has to protect the derma rollers from physical damage, contamination, and ecological aspects such as humidity and temperature variations. This is important to keep the sterility and efficiency of the product until it gets to the customer.
Security Considerations and Challenges
Among the substantial challenges in derma roller manufacturing is ensuring that the product packaging is tamper-proof and child-resistant. This calls for using sophisticated products and securing innovations. In addition, clear labeling is important to give individuals needed information such as usage directions, safety and security warnings, and expiry days. Any oversight in these areas can lead to security threats and possible regulatory issues.
Product Selection for Packaging
The option of packaging products is an additional essential facet. Manufacturers should choose materials that are sturdy and non-reactive with the derma roller parts. This frequently includes the use of medical-grade plastics or various other risk-free products that abide by international safety requirements, making sure that the product continues to be uncontaminated and secure for usage.
Stabilizing Cost and Quality
While ensuring safety, security, and quality, producers additionally face the difficulty of managing expenses. Top-quality packaging products and advanced security features can significantly increase manufacturing costs. Therefore, finding a balance in between cost-effectiveness and uncompromised safety is a constant obstacle in derma roller manufacturing.
Technical Innovations in Packaging
Current developments in packaging technology offer services to some of these obstacles. Smart product packaging, which includes features like QR codes for authentication and tracking, is becoming increasingly prominent. These technologies not only enhance safety and security but also boost consumer trust and satisfaction.
Challenges in Derma Roller Manufacturing: Price Management and Production Efficiency
In attending to the difficulties in derma roller production, expense administration, and production effectiveness play critical roles. Stabilizing these elements ensures that manufacturers stay affordable while preserving premium standards. Here, I will certainly describe several of the crucial techniques and considerations included.
Maximizing Material Usage
One of the key means to handle prices is through the optimization of material usage. Selecting the best materials that provide sturdiness and performance, while lessening waste, is critical. This includes sourcing needles and roller parts from dependable providers who use competitive prices without endangering on quality.
Streamlining Production Processes
Enhancing manufacturing efficiency entails streamlining manufacturing processes. Executing lean manufacturing strategies can substantially decrease waste and enhance workflow. This frequently involves investing in innovation that automates repeated jobs, thereby reducing labor expenses and decreasing human error.
Investing in Technology
Technological innovations can considerably aid in getting rid of the challenges in derma roller manufacturing. By taking on cutting-edge equipment and software applications, suppliers can boost precision and rate of production. This not only lowers prices but also boosts the total top quality of the last product.
Efficient Supply Chain Management
Taking care of the supply chain efficiently is an additional vital aspect. This entails keeping solid relationships with suppliers and guaranteeing prompt procurement of products. A well-managed supply chain can lead to decreased preparations and reduced inventory prices.
Price Analysis and Budgeting
Routine price evaluation and budgeting are essential for identifying areas where expenditures can be lessened. This includes analyzing manufacturing costs, labor expenditures, and overheads. By continuously monitoring these factors, producers can make enlightened decisions that enhance success.
Expense Management Strategy | Advantages |
---|---|
Material Optimization | Minimizes waste and reduces material costs |
Streamlined Processes | Boosts efficiency and decreases labor expenses |
Technological Investment | Enhances precision and rate, reducing total costs |
Supply Chain Management | Lowers preparations and inventory costs |
Cost Analysis and Budgeting | Educates tactical choices for greater success |
In summary, addressing the challenges in derma roller manufacturing requires a detailed approach to cost administration and manufacturing effectiveness. By concentrating on these areas, suppliers can guarantee they continue to be competitive while providing high-quality products to the market.
Challenges in Derma Roller Manufacturing: Technologies and Technological Advancements in Manufacturing
In the realm of derma roller production, continuous development, and technological improvements play a vital role in getting over existing challenges. As the demand for high-quality derma rollers rises, makers are concentrating on integrating sophisticated innovations to enhance production efficiency and item quality.
Advanced Materials and Coatings
The expedition of new materials and finishings is a considerable location of innovation. Manufacturers are experimenting with biocompatible materials that not only ensure security but also improve the toughness of the needles. Advanced coverings, such as antimicrobial layers, are being created to improve health and decrease the risk of infections.
Automation and Precision Engineering
Automation in needle manufacturing is changing the market. High-precision devices are being made use of to achieve regular needle intensity and placement, resolving the vital challenges in derma roller manufacturing. This technological development guarantees uniformity and minimizes human error, therefore boosting manufacturing efficiency.
3D Printing and Prototyping
The usage of 3D printing technology permits quick prototyping and testing of new layouts. This advancement allows suppliers to try out different arrangements and swiftly bring brand-new items to market. The adaptability of 3D printing also sustains customization, catering to specific customer requirements and preferences.
Data-Driven Manufacturing
Information analytics and IoT (Internet of Things) combination are revolutionizing manufacturing processes. By collecting and assessing information in real-time, suppliers can maximize procedures, anticipate maintenance needs, and minimize downtime. This data-driven technique enhances overall production efficiency and addresses cost-monitoring challenges.
Table: Key Technological Advancements
Technology | Benefits |
---|---|
Advanced Materials | Boosted longevity and security |
Automation | Boosted accuracy and effectiveness |
3D Printing | Quick prototyping and personalization |
Information Analytics | Enhanced procedures and price decrease |
In summary, staying at the leading edge of technological developments is crucial for attending to the crucial challenges in derma roller manufacturing. By embracing these developments, producers can not just improve product quality and safety but likewise improve their affordable side in the market.
FAQs on Challenges in Derma Roller Manufacturing Process
What are the main challenges in derma roller manufacturing?
The primary challenges include ensuring precision in needle production, maintaining stringent sterilization standards, selecting appropriate materials, and adhering to regulatory compliance. Each of these areas requires meticulous attention to detail and robust quality control measures.
Why is material selection crucial in derma roller manufacturing?
Material selection is vital because it affects the durability, safety, and effectiveness of the derma rollers. Manufacturers must balance cost with quality, selecting materials that meet regulatory standards and consumer expectations.
How do manufacturers ensure the precision of needles in derma rollers?
Precision is achieved through advanced manufacturing techniques like laser cutting and micro-machining. Rigorous quality assurance testing ensures each needle meets the required specifications for sharpness and uniformity.
What sterilization methods are used in derma roller manufacturing?
Common methods include steam sterilization, ethylene oxide (EO) sterilization, and gamma radiation. Each method is chosen based on its effectiveness and compatibility with the materials used in derma rollers.
How do regulatory requirements impact derma roller manufacturing?
Regulatory requirements ensure the safety and efficacy of derma rollers. Manufacturers must comply with standards from bodies like the FDA and CE, which involve thorough testing and documentation.
What role does packaging play in derma roller manufacturing?
Packaging is crucial for protecting the product from damage and contamination. It must be tamper-proof and include clear labeling for user safety, balancing these requirements with cost-effectiveness.
How do manufacturers manage production costs and efficiency?
Cost management involves optimizing material usage, streamlining production processes, and investing in technology. Effective supply chain management and regular cost analysis also play key roles in maintaining efficiency.
What technological advancements are shaping the future of derma roller manufacturing?
Innovations include the use of advanced materials and coatings, automation in needle production, 3D printing for rapid prototyping, and data-driven manufacturing processes. These advancements enhance efficiency and product quality.
References
- DermarollerInsights, Derma Roller Precision: Overcoming Manufacturing Challenges, https://www.dermarollerinsights.com/manufacturing-precision-challenges
- SkinTechJournal, Quality Control in Derma Roller Production, https://www.skintechjournal.com/quality-control-derma-roller-production
- HealthDeviceNews, Understanding Regulatory Compliance in Derma Roller Manufacturing, https://www.healthdevicenews.net/regulatory-compliance-derma-roller
- MedTechToday, Sterilization Techniques in Derma Roller Manufacturing, https://www.medtechtoday.org/sterilization-derma-rollers
- ManufacturingMaterialsGuide, Material Sourcing Challenges for Derma Rollers, https://www.manufacturingmaterialsguide.com/derma-roller-sourcing
- SkinCareManufacturing, Why Needle Sharpness Matters in Derma Rollers, https://www.skincaremanufacturing.com/needle-sharpness-derma-rollers
- ProductionEfficiencyDaily, Balancing Cost and Quality in Derma Roller Production, https://www.productionefficiencydaily.com/cost-vs-quality-derma-roller
- PackagingToday, Innovations in Derma Roller Packaging Solutions, https://www.packagingtoday.com/derma-roller-packaging-innovations
- DeviceManufactureReview, Common Pitfalls in Derma Roller Manufacturing, https://www.devicemanufacturereview.com/derma-roller-pitfalls
- ManufacturingTechDigest, Automating Precision in Derma Roller Production, https://www.manufacturingtechdigest.com/derma-roller-automation-precision
- HealthCareDeviceUpdates, The Impact of Regulatory Changes on Derma Roller Manufacturing, https://www.healthcaredeviceupdates.com/regulatory-impact-derma-rollers
- MedicalDeviceCleanroom, Ensuring Sterility in Derma Roller Products, https://www.medicaldevicecleanroom.com/sterility-derma-roller-products
- MicroNeedlingTechnology, Challenges in Consistent Needle Length for Derma Rollers, https://www.microneedlingtechnology.com/needle-length-challenges
- MedTechManufacturersForum, How to Source High-Quality Derma Roller Materials, https://www.medtechmanufacturersforum.com/source-derma-roller-materials
- ProductionCostStrategies, Overcoming Cost Barriers in Derma Roller Manufacturing, https://www.productioncoststrategies.com/overcome-cost-barriers-derma-rollers
- TechnologyInManufacturing, Technological Solutions to Derma Roller Manufacturing Challenges, https://www.technologyinmanufacturing.com/tech-solutions-derma-rollers