Table of Contents
ToggleLatest Innovations Technologies in Derma Roller Production
This article delves into the transformative advancements in technologies in derma roller production. From innovative materials to precision manufacturing techniques, these developments promise enhanced safety, efficiency, and user experience.
Integration of Smart Technologies
As an expert in the field, I highlight the integration of smart technologies, sustainable practices, and customization trends that are redefining derma roller production. These cutting-edge innovations not only meet consumer demands but also set new standards for quality and performance in skincare solutions.
Technologies in Derma Roller Production Materials
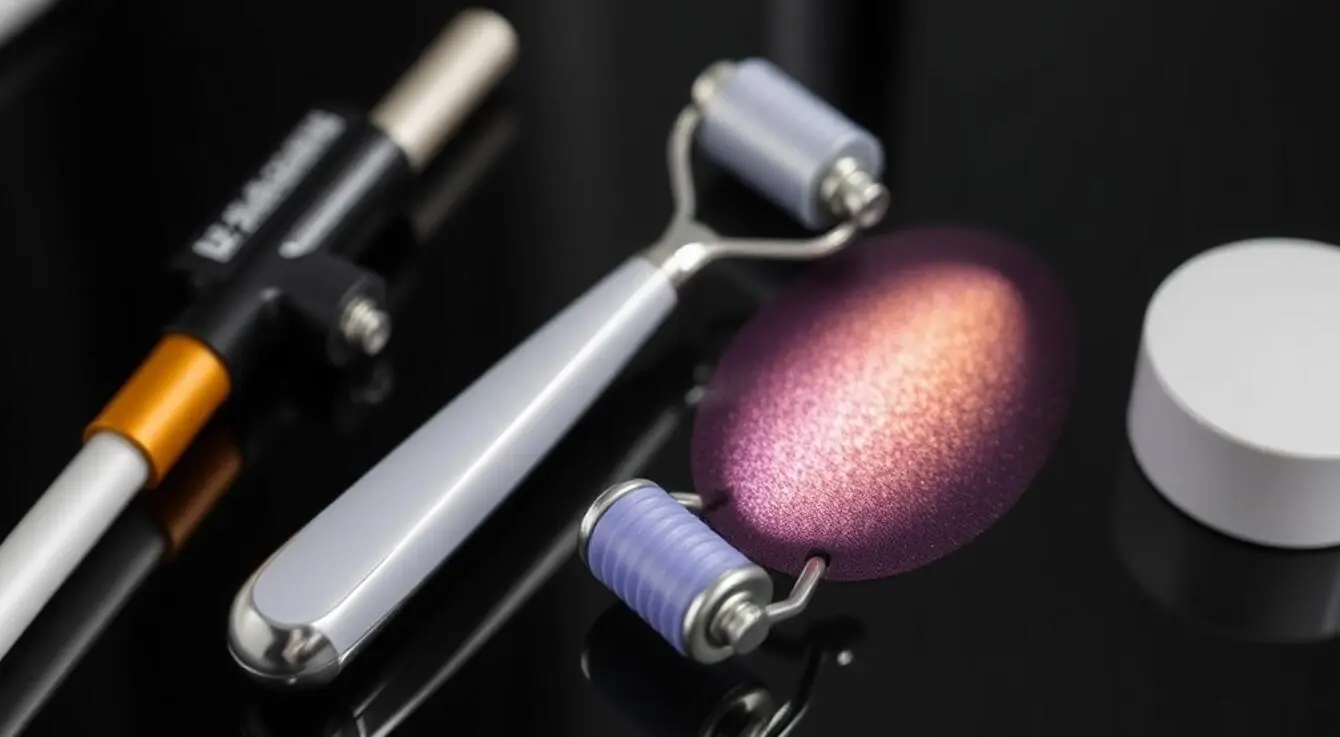
In the last few years, modern technologies in derma roller production have observed substantial advancements, particularly in the products used. These technologies are driven by the requirement for improved performance, safety, and efficiency in skin treatment applications. As an expert in the area, I have observed a change in the direction of the use of much more innovative products that provide boosted longevity and customer experience.
Biocompatible Materials
One of the most significant fads is the fostering of biocompatible products. These products are created to lessen adverse reactions and ensure the security of users. For example, medical-grade stainless steel and titanium are currently typically utilized for needle construction as a result of their premium toughness and resistance to deterioration.
Product | Benefits |
---|---|
Stainless steel | Sturdiness, Corrosion Resistance |
Titanium | Toughness, Biocompatibility |
Polymer Advancements
In addition to metals, there has been a significant rise in the use of advanced polymers in derma rollers. These materials offer flexibility and can be precisely engineered to possess unique properties that enhance the performance of the devices. Polymers like polycarbonate and medical-grade silicone are increasingly used to create components that are not only lightweight but also ergonomic, improving the overall user experience.
Polymer | Feature |
---|---|
Polycarbonate | Light-weight, Impact Resistance |
Medical-grade Silicone | Versatility, Comfort |
Coating Technologies
Finishing technologies have evolved to improve the efficiency of derma rollers. Anti-microbial layers are progressively applied to needles to decrease the danger of infection and enhance health. In addition, some derma rollers are currently furnished with coatings that promote smoother skin penetration and minimize pain during usage.
The combination of these innovative materials in derma roller manufacturing not only raises the top quality of the products but also aligns with the growing demand for personalized and risk-free skincare solutions. As we continue to discover these sophisticated innovations, it is apparent that the future of derma roller materials holds enormous possibilities for further improvements and advancements.
Advanced Technologies for Derma Roller Production
In the realm of derma roller manufacturing, progressed manufacturing methods have become critical in boosting both the efficiency and top quality of these skin care devices. The assimilation of cutting-edge technologies has reinvented the production process, making sure of precision and integrity at every phase.
Accuracy Machining
One of the primary methods used is accurate machining. This approach permits the careful crafting of derma roller components, particularly the needles, which require specific requirements to guarantee ideal performance. By using computer system mathematical control (CNC) equipment, suppliers can attain unmatched precision, dramatically lowering the margin for error and enhancing the overall quality of the product.
Shot Molding
Another critical method is injection molding, which is commonly used in the production of derma roller handles and cases. This process involves infusing molten products into mold and mildew to develop and get rid of complicated geometries. The usage of premium polymers and progressed molding modern technologies guarantees that the final products are both long-lasting and lightweight, meeting the strict demands of modern consumers.
Laser Cutting and Welding
Laser cutting and welding are integral to the manufacturing procedure, especially in the assembly of metal elements. These strategies supply high precision and rate, enabling the seamless assimilation of various parts without endangering their structural integrity. The application of laser technologies in derma roller production not only improves the aesthetic allure of the rollers but also adds to their capability and long life.
3D Printing
The development of 3D printing has introduced brand-new opportunities in the modification and prototyping of derma rollers. This technology enables makers to swiftly generate and test new styles, helping with innovation and lowering the time to market for brand-new items. The flexibility supplied by 3D printing is especially useful in accommodating the expanding need for customized skin care solutions.
Including these sophisticated technologies in derma roller production not only raises the high quality of the items but also aligns with the progressing assumptions of customers who seek both efficiency safety and security in their skin treatment tools. As innovations in derma roller manufacturing remain in development, the market is poised to deliver much more refined and effective solutions to fulfill the diverse requirements of individuals worldwide.
Precision Engineering in Derma Roller Needle Design
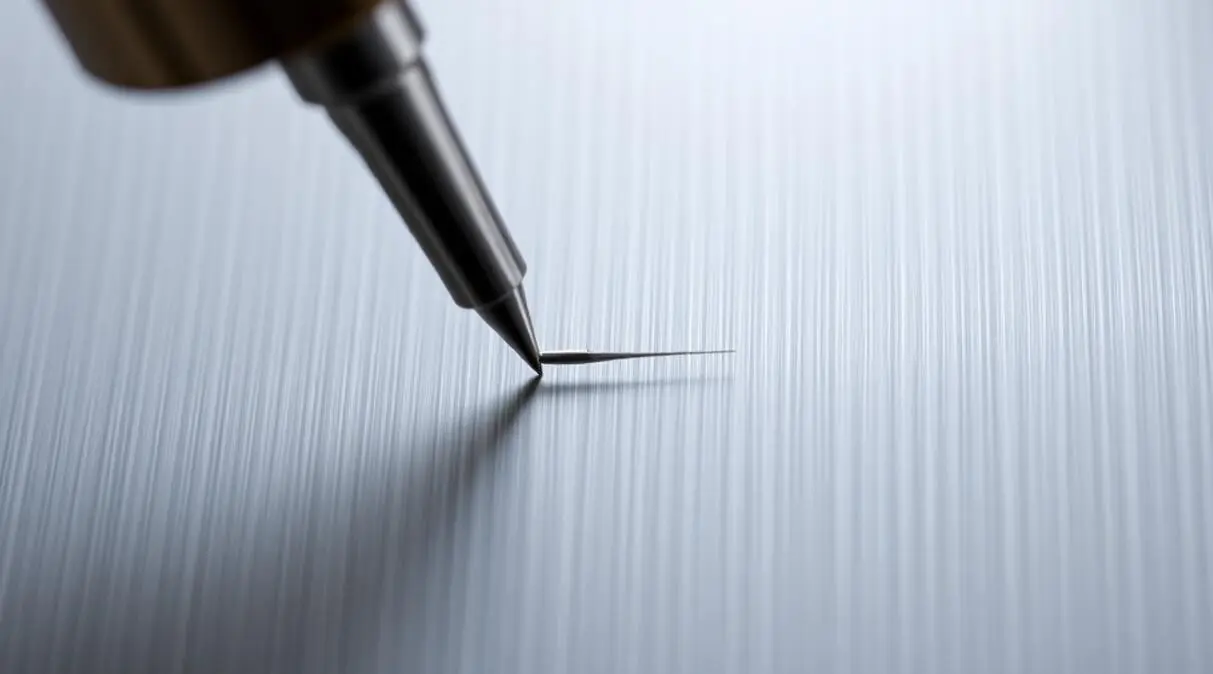
In the realm of technologies in derma roller production, precision engineering plays a pivotal role in the style and development of needles. The elaborate nature of these devices necessitates meticulous attention to detail to ensure both efficiency and security. The primary purpose is to attain optimal needle sharpness and positioning, which are essential for improving the customer’s experience and maximizing the device’s effectiveness.
Innovative Materials for Needle Design
The selection of materials is a basic facet of precision design in needle design. State-of-the-art stainless steel and titanium are generally used because of their sturdiness and resistance to deterioration. These materials add to the durability and integrity of the derma rollers, guaranteeing they keep their efficiency over time.
Material | Benefits |
---|---|
Stainless-steel | Durability, Corrosion Resistance |
Titanium | Light-weight, High Strength |
Advanced Technologies in Derma Roller Production
Advanced technologies in derma roller production are used to accomplish the specific specs needed for needle manufacturing. Laser cutting and micro-machining are widespread techniques that permit exact needle dimensions and shapes. These modern technologies boost the accuracy and uniformity of needle manufacturing, ensuring uniformity across sets.
Layout Considerations for Needle Configuration
Configuration and positioning of needles are important for effective derma roller capability. Engineers concentrate on the number of needles, their setup, and the angle of infiltration to maximize skin contact and reduce discomfort. A well-engineered needle arrangement ensures that the derma roller supplies consistent outcomes while maintaining customer convenience.
Quality Control in Derma Roller Needle Production
Quality control processes are integral to keeping high requirements in needle production. Strenuous screening and inspection methods are executed to verify needle sharpness, placement, and material integrity. These procedures aid in determining any inconsistencies from the preferred requirements, making certain that only top-quality needles reach the market.
Top Quality Assurance Process | Function |
---|---|
Sharpness Testing | Make Sure Optimal Performance |
Placement Inspection | Verify Needle Configuration |
Product Integrity Check | Maintain Durability |
With the assimilation of precision engineering and cutting-edge innovation technologies in derma roller production, derma roller manufacturers can supply items that satisfy the highest requirements of top quality and efficiency. This concentration on precision enhances the efficacy of derma rollers and elevates the general user experience.
Automation Technologies in Derma Roller Production
In the swiftly progressing landscape of modern technologies in derma roller production, automation has emerged as a pivotal part of improving performance and precision. The assimilation of automated systems in the assembly line has transformed the method derma rollers are produced, guaranteeing consistency and decreasing human error.
Robot Assembly Systems
Robotic systems have ended up being a foundation in the assembly of derma rollers. These systems are developed to take care of intricate tasks with a high degree of precision, such as lining up and connecting needles to the roller heads. Using robotics not only accelerates the manufacturing process but also preserves a uniform top quality throughout all items, which is vital in the sensitive area of skin care.
Automated Quality Inspection
Another significant improvement is the execution of computerized quality evaluation systems. These technologies make use of high-resolution cameras and sensors to find any type of problems or abnormalities in the derma rollers throughout the setup process. By identifying issues early, makers can guarantee that just products satisfying the finest standards reach the marketplace.
Streamlining Production with AI
Artificial intelligence plays a crucial role in optimizing the assembly line. AI-driven analytics are utilized to check and readjust the manufacturing circulation in real time, guaranteeing optimum performance and minimizing downtime. This level of precision in assembly administration is a testimony to the advanced modern technologies in derma roller production that are being embraced throughout the market.
Benefits of Automation
The change towards automation in derma roller setting up brings many benefits. Mainly, it permits a substantial reduction in manufacturing costs as a result of decreased labor needs and lessened waste. Besides, it enhances the scalability of operations, making it possible for makers to fulfill boosting needs without jeopardizing quality or effectiveness.
As we continue to discover the most recent technologies in derma roller production, automation stands apart as a transformative force, establishing new criteria for quality and advancement in the industry.
Top Quality Control Technologies in Derma Roller Production
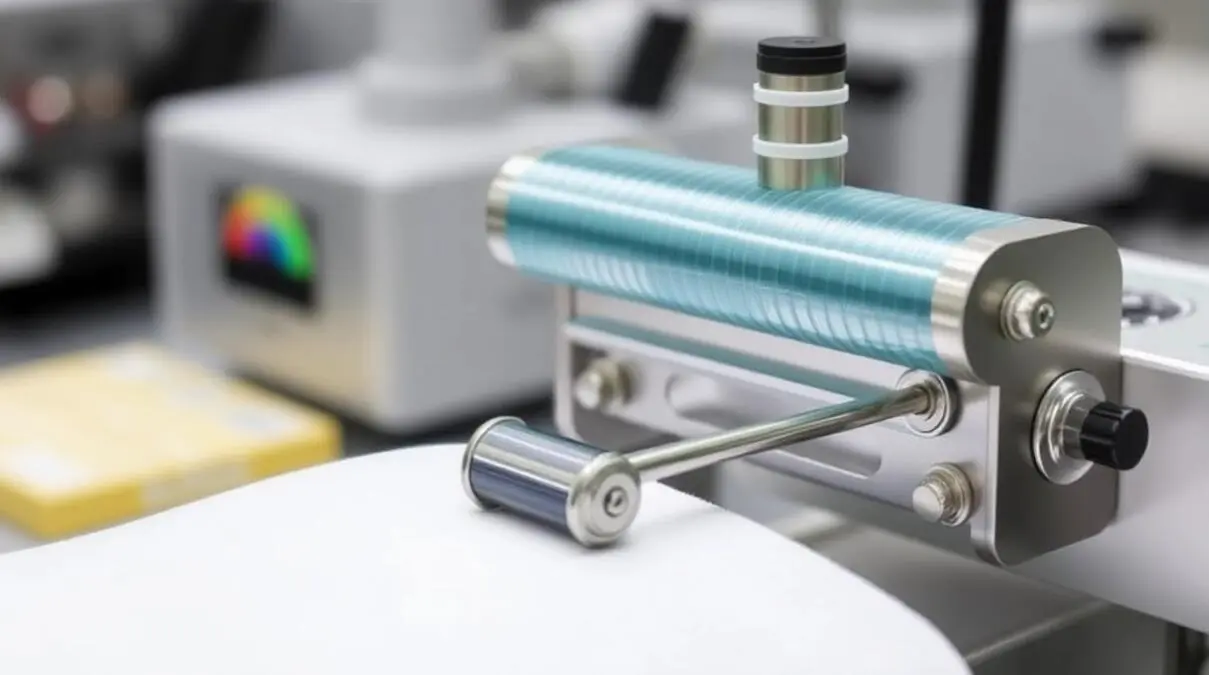
Ensuring the highest possible standards of top quality control in derma roller production is vital for both producers and customers. Advanced innovation technologies in derma roller production have led the method for a lot more exact and effective top-quality guarantee procedures. These innovations help in preserving the stability and safety of the items, which is of paramount importance in the skincare market.
Automated Inspection Systems
One of the crucial improvements in top quality control is using automatic evaluation systems. These systems use high-resolution electronic cameras and sensors to detect any type of imperfections or incongruities in the derma rollers. By utilizing equipment vision innovation, producers can ensure that each roller meets the rigorous criteria needed for risk-free skin application.
Evaluation Technology | Advantages |
---|---|
Equipment Vision | High accuracy, uniformity, and speed |
High-resolution Cameras | Detailed defect discovery |
Sensing units | Accurate measurement of needle alignment |
Real-time Monitoring and Feedback
Real-time surveillance systems are essential to preserving top quality during production. These systems provide instant feedback on the assembly line, allowing for instant changes and corrections. This proactive strategy minimizes waste and makes certain that only items meeting the highest possible standards continue to the following phase of manufacturing.
Information Analytics and Reporting
Information analytics plays a considerable role in boosting quality assurance. By analyzing production data, producers can recognize patterns and potential problems before they intensify. Comprehensive coverage devices use an understanding of production performance and quality metrics, allowing constant improvement in derma roller manufacturing processes.
Data Analytics Tool | Feature |
---|---|
Trend Analysis | Identify manufacturing patterns and anomalies |
High quality Metrics | Procedure product conformity and performance |
Coverage Tools | Give insights for procedure optimization |
Compliance with Safety Standards
Sticking to global safety and top-quality requirements is non-negotiable in derma roller production. Technologies in derma roller production guarantee conformity with guidelines such as ISO criteria, which regulate the top quality and safety of medical gadgets. Routine audits and certifications, even more, reinforce the commitment to creating secure and effective derma rollers.
Lasting Practices in Derma Roller Manufacturing
Eco-Friendly Material Selection
In the pursuit to improve sustainability within the derma roller market, one of the leading considerations is the choice of green products. Producers are progressively going with biodegradable and recyclable products in the manufacturing of derma rollers. This change not only minimizes the environmental footprint but also lines up with customer needs for even more eco-conscious products.
Energy-Efficient Manufacturing Processes
The assimilation of energy-efficient technologies in derma roller production is another critical action in the direction of sustainability. By embracing sophisticated equipment that decreases energy usage, manufacturers can dramatically decrease their carbon emissions. This strategy profits the environment and reduces operational expenses, creating a win-win scenario for manufacturers and the world alike.
Waste Reduction Strategies
Applying efficient waste administration techniques is critical in sustainable derma roller production. Firms are now concentrating on minimizing waste at every phase of manufacturing, from lessening excess product use to reusing manufacturing scraps. These initiatives are matched by the fostering of lean manufacturing concepts, which enhance processes and reduce waste.
Water Conservation Techniques
Water is a crucial resource in production, and its preservation is a vital element of sustainable technologies in derma roller production, innovative water-saving strategies are being released to reduce water usage. This consists of the recycling of water within manufacturing processes and making use of closed-loop systems that substantially lower water wastage.
Commitment to Ethical Labor Practices
Sustainability extends past ecological considerations to incorporate honest labor methods. Making certain reasonable earnings, securing working problems, and ensuring the wellness of employees are indispensable to sustainable derma roller production. Firms committed to these concepts are adding to social sustainability and boosting their track record and consumer trust.
Innovative Packaging Solutions
Product packaging is a crucial element of sustainability in derma roller manufacturing. The sector is relocating towards utilizing recyclable and minimalistic product packaging remedies that lower waste and ecological impact. By employing biodegradable materials and creating product packaging that minimizes excess, makers are making strides in lasting product packaging innovations.
Collaborative Efforts and Industry Partnerships
Partnership within the sector is essential for progressing lasting methods. Derma roller manufacturers are increasingly developing partnerships with environmental organizations and taking part in industry-wide initiatives targeted at advertising sustainability. These collective initiatives are critical for sharing knowledge, sources, and modern technologies that drive the industry toward a much more sustainable future.
Customization and Personalization Trends in Derma Rollers
The trend of derma roller manufacturing is evolving rapidly, with customization and personalization becoming substantial patterns. As consumers significantly seek items tailored to their specific needs, suppliers are leveraging innovative innovations to offer an extra-individualized experience.
Material Customization
One of the primary locations of modification remains the option of materials. Customers can currently select derma rollers made from a range of products, each offering unique advantages. Choices include titanium, stainless steel, and also gold-plated needles, providing different skin kinds and levels of sensitivities.
Product | Advantages |
---|---|
Titanium | Sturdy and less susceptible to bending |
Stainless-steel | Immune to deterioration and cost-effective |
Gold-Plated | Hypoallergenic and elegant allure |
Needle Length Variability
Another important aspect of personalization is the ability to select needle sizes. Different skin problems require different needle motifs, and manufacturers are now providing derma rollers with interchangeable heads to suit this demand. This flexibility enhances the performance of treatments, enabling users to target specific issues such as acne scars or fine lines.
Layout and Aesthetics
Past capability and the aesthetic appeals of derma rollers are seeing a change. Consumers can pick from an array of shades, ergonomic styles, and also personalized engravings. This trend enhances the individual experience and straightens with the growing demand for items that mirror individual styles and preferences.
Assimilation with Smart Technologies
Integrating smart modern technologies right into derma rollers is a rising trend. Some models now feature sensors that give feedback on the stress applied throughout use, making certain optimum results and decreasing the danger of skin damage. These technologies represent considerable innovation in innovations in derma roller production, offering customers a more enlightened and regulated skincare routine.
Future Directions
As the need for customized skin care services continues to grow, we can anticipate more developments in derma roller modification. Future advancements may include AI-driven referrals for needle arrangements based on private skin evaluation, further enhancing the efficacy and allure of these gadgets.
Future Prospects in Derma Roller Technology Development
As we look towards the future of derma roller technology, several appealing avenues are emerging that can significantly enhance the efficacy and functionality of these gadgets. The continual development of technologies in derma roller production is leading the way for developments that can redefine skin care regimens and outcomes.
Integration of Smart Technology
One of the most amazing leads is the integration of smart technology into derma rollers. This might involve making use of sensors to monitor skin conditions in real time, supplying individuals with immediate comments on their skin’s response to therapy. Such developments can enable personalized therapy strategies tailored to the one-of-a-kind demands of each individual’s skin.
Nanotechnology Applications
Nanotechnology holds the potential to reinvent derma roller efficiency. By integrating nanoparticles, it could be possible to enhance the delivery of active ingredients into the skin, improving the overall efficiency of treatments. This could result in better-targeted treatments and faster outcomes for individuals.
Biodegradable Materials
In response to expanding ecological issues, the growth of sustainable techniques in derma roller production is likely to play an important role. Using naturally degradable materials can reduce the ecological influence of derma roller manufacturing and disposal, straightening with more comprehensive sustainability goals.
Modification and Personalization
The fad towards customization and personalization is anticipated to proceed, with advancements of technologies in derma roller production permitting even more tailored items. This might include adjustable needle sizes and customized roller configurations to provide to different skin kinds and treatment locations.
Potential Developments
Modern technology | Prospective Impact |
---|---|
Smart Sensors | Real-time skin analysis and feedback |
Nanotechnology | Boosted shipment of energetic ingredients |
Biodegradable Materials | Decreased environmental influence |
Personalization Options | Individualized treatment experiences |
To conclude, the future of advanced technologies in derma roller production looks encouraging, with various chances for advancements that could change the industry. By welcoming these innovations, manufacturers can continue to satisfy the evolving needs of consumers, giving much more reliable, lasting, and personalized skincare services.
FAQs on Exploring the Latest Technologies in Derma Roller Production
1. What are the latest technologies in derma roller production?
Modern derma roller production involves technologies like precision laser cutting, microneedle etching, and electro-polishing, ensuring that needles are sharp, uniform, and safe for skin penetration.
2. How do microneedle technologies in derma roller production improve treatment results?
Microneedle technologies help create ultra-sharp, consistent needles that penetrate the skin at controlled depths, improving the effectiveness of derma rollers in collagen stimulation and skin rejuvenation.
3. What are the key material technologies used in derma roller production?
Material technologies in derma roller production focus on using medical-grade stainless steel or titanium for needles, ensuring strength, durability, and resistance to corrosion, while also being safe for skin contact.
4. How do advancements in needle length technologies in derma roller production affect safety?
Advanced needle length technologies ensure that needles are manufactured to precise, consistent lengths, which is critical for preventing skin damage and ensuring effective treatments.
5. Why are laser cutting and electro-polishing technologies important in derma roller production?
Laser cutting and electro-polishing technologies in derma roller production ensure that needles are sharp, precise, and smooth, reducing skin irritation and improving safety during use.
6. How does sterilization technology play a role in derma roller production?
Sterilization technologies in derma roller production, such as gamma radiation and ethylene oxide, ensure that each roller is free from harmful bacteria, making them safe for use on the skin.
7. How does nanotechnology improve derma roller production?
Nanotechnology in derma roller production enhances the sharpness and durability of needles, allowing for finer needle tips and improved skin penetration, leading to more effective treatments.
8. What quality control technologies are involved in derma roller production?
Quality control technologies in derma roller production, such as automated inspection systems, ensure that each roller meets strict standards for needle alignment, sharpness, and length, providing a consistent and safe user experience.
9. What recent advancements in technologies in derma roller production are enhancing performance?
Recent advancements in derma roller production technologies include improvements in micro-etching techniques, hypoallergenic coatings, and automated manufacturing processes, all of which enhance the durability, safety, and comfort of the rollers.
10. How are sustainable technologies incorporated into derma roller production?
Sustainable technologies in derma roller production focus on using recyclable materials, minimizing plastic components, and optimizing manufacturing processes to reduce waste and improve the environmental footprint of the products.
References
- Derma Roller Research, “The Evolution of Microneedling and Derma Roller Production,” https://www.dermarollerresearch.com/evolution-microneedling
- Healthline, “What to Know About Derma Rollers and How They’re Made,” https://www.healthline.com/health/derma-roller-production
- Skincare Innovation, “Material Science in Modern Derma Roller Manufacturing,” https://www.skincareinnovation.com/material-science-derma-rollers
- Science Daily, “How Microneedling Technology Is Transforming Skincare,” https://www.sciencedaily.com/releases/microneedling-skincare-technology
- Medical News Today, “The Role of Sterilization in Safe Derma Roller Production,” https://www.medicalnewstoday.com/sterilization-derma-rollers
- Dermatology Times, “Exploring the Benefits of Titanium Needles in Derma Rollers,” https://www.dermatologytimes.com/titanium-needles-derma-rollers
- Allure, “Why Laser Cutting Is Essential in Derma Roller Manufacturing,” https://www.allure.com/laser-cutting-derma-roller
- Advanced Dermatology, “Electro-Polishing and Its Role in Derma Roller Safety,” https://www.advanceddermatology.com/electro-polishing-derma-rollers
- Cosmetics Business, “Advancements in Eco-Friendly Derma Roller Production,” https://www.cosmeticsbusiness.com/eco-friendly-derma-rollers
- Beauty Tech News, “The Importance of Needle Length in Derma Roller Effectiveness,” https://www.beautytechnews.com/needle-length-derma-rollers
- Skin Health Journal, “Microneedle Technology: Precision in Derma Roller Production,” https://www.skinhealthjournal.com/microneedle-technology
- Modern Aesthetics, “How Quality Control in Production Ensures Derma Roller Safety,” https://www.modernaesthetics.com/quality-control-derma-rollers
- Cosmetic Formulators, “Nanotechnology in the Production of Derma Rollers,” https://www.cosmeticformulators.com/nanotechnology-derma-rollers
- The Journal of Aesthetic Medicine, “How Sterilization Technologies Protect Derma Roller Users,” https://www.aestheticmedicinejournal.com/sterilization-derma-rollers
- Future of Beauty, “Sustainable Materials in Derma Roller Manufacturing,” https://www.futureofbeauty.com/sustainable-derma-rollers
- Skincare Science Hub, “How Automated Technologies Enhance Derma Roller Production,” https://www.skincaresciencehub.com/automated-derma-roller-production