Table of Contents
ToggleWhat is The Derma Roller Manufacturing Standards
In the intricate domain of derma roller manufacturing standards, maintaining consistency across every batch is crucial. This article explores the meticulous processes involved, including strict material selection, advanced precision engineering, and rigorous testing protocols, ensuring that each derma roller adheres to the highest safety and efficacy standards.
Quality Control and Technology
Discover how derma roller manufacturers uphold derma roller manufacturing standards through rigorous quality control, advanced technology, and sustainable practices. Learn about the importance of skilled workforce training and regulatory compliance in delivering reliable skincare tools that consumers can trust.
Components of Derma Roller Manufacturing
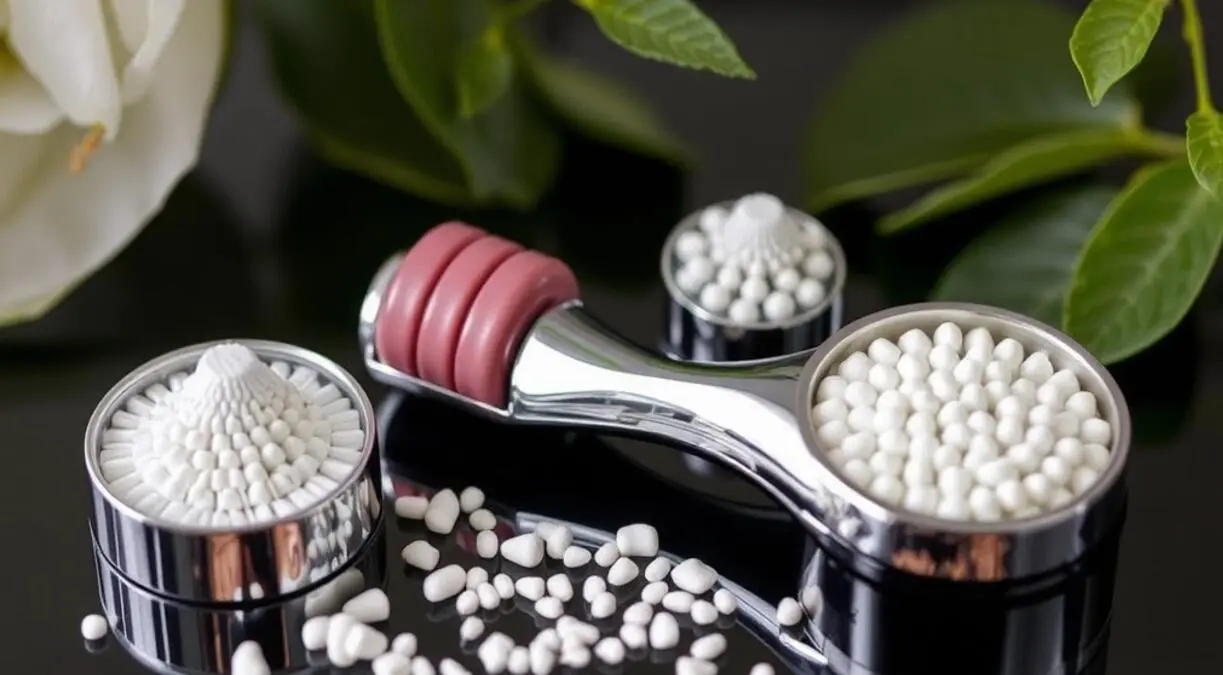
In the world of derma roller manufacturing, keeping high requirements in every batch is crucial to ensure product efficacy and safety. This entails a meticulous strategy to the choice of products, accuracy design, and stringent quality checks.
Material Selection
The foundation of a top quality derma roller depends on the careful choice of products. The derma roller needles, typically made from stainless steel or titanium, should satisfy details solidity and rust resistance requirements to guarantee longevity and safety and security. The deal with and roller body should be composed of medical-grade plastic to stop any unfavorable skin reactions.
Element | Material | Specifications |
---|---|---|
Needles | Stainless Steel or Titanium | Solidity, Corrosion Resistance |
Take care of | Medical-Grade Plastic | Biocompatibility |
Accuracy Engineering
Precision in production is very important. The needles must be evenly lined up and safely affixed to the roller to ensure regular efficiency across all devices. Advanced machinery and innovation are utilized to accomplish the needed accuracy, reducing the margin of mistake and improving the derma roller manufacturing standards.
Quality Control of Derma Rollers
Executing a durable quality control procedure is crucial to preserve the integrity of every batch. This includes rigorous screening of the mechanical homes of the needles, along with the overall architectural honesty of the derma roller. Quality checks need to be performed at numerous phases of production to recognize and remedy any kind of inconsistencies from the established standards.
High Quality Check Stage | Focus Area |
---|---|
Product Inspection | Needle Hardness, Plastic Quality |
Setting up Verification | Needle Alignment, Attachment Security |
Final Product Testing | Structural Integrity, Performance Consistency |
By sticking to these crucial parts, producers can ensure that every derma roller generated fulfills the highest derma roller manufacturing standards, offering customers with a trustworthy and reliable skincare tool.
Applying Quality Control Measures
Guaranteeing the highest derma roller manufacturing standards calls for a robust quality assurance system that meticulously checks every stage of production. This is crucial in supplying products that are both risk-free and effective for end-users. Below are the essential parts and methods for executing efficient quality assurance actions in derma roller manufacturing.
Resources Inspection
Quality assurance starts with the inspection of resources. Each batch of products should be rigorously evaluated to ensure they meet predefined requirements. This includes monitoring for any type of pollutants or problems that can compromise the high quality of the derma rollers.
In-Process Monitoring
During the manufacturing process, continuous monitoring is vital. Implementing real-time checks at numerous phases assists in identifying any type of discrepancies from the preferred standards. This consists of monitoring the precision of needle alignment and the honesty of the roller mechanisms.
Final Product Testing
As soon as the derma rollers are set up, they should undertake detailed testing to guarantee they meet all safety and efficiency requirements. This includes longevity examinations, needle intensity assessments, and making sure the rollers are without any kind of production defects.
Executing Statistical Process Control
Statistical Process Control (SPC) is a crucial tool in preserving derma roller manufacturing standards. By assessing information gathered during production, makers can determine fads and variations, enabling them to make educated choices to maximize the manufacturing procedure.
Documentation and Traceability
Preserving in-depth documents of every batch created is vital. This documents needs to include details on resources resources, production procedures, and quality checks carried out. This ensures traceability and responsibility, which are essential for regulatory conformity and quality assurance.
Routine Audits and Reviews
Performing normal audits and reviews of the manufacturing processes assists in identifying areas for improvement. These audits needs to be both interior and exterior, giving an objective assessment of the high quality control measures in location.
By implementing these quality assurance measures, manufacturers can consistently maintain the greatest derma roller manufacturing standards, guaranteeing that every batch generated is of exceptional high quality and dependability.
Embracing Industry Best Practices
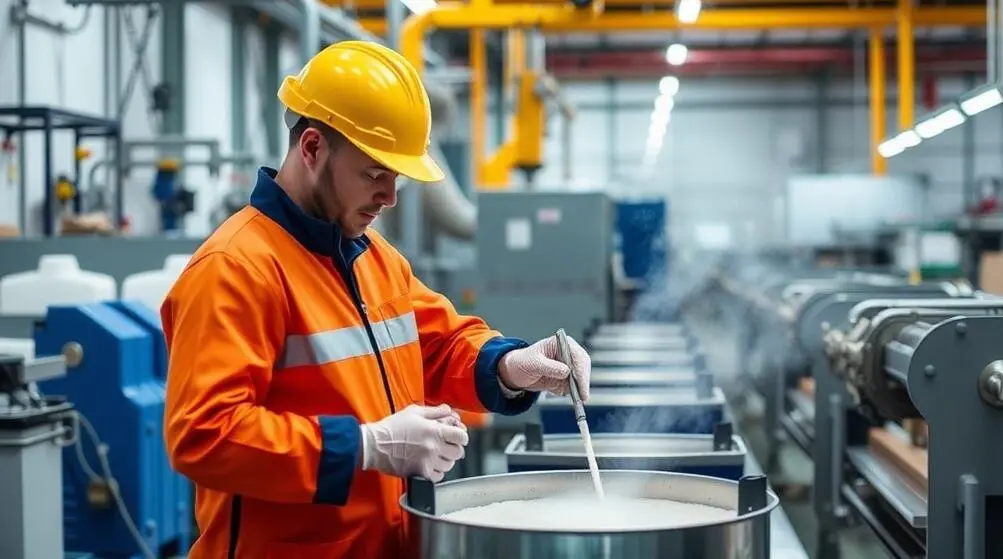
To ensure that every batch of derma rollers meets the highest manufacturing standards, it is essential to adopt industry best practices. These approaches not only improve product quality but also build trust and credibility with consumers. Key areas where these practices must be implemented include material selection, precision manufacturing, rigorous quality control, and adherence to safety and regulatory standards.
Material Selection
Picking the appropriate materials is fundamental to keeping derma roller production standards. High-quality medical-grade stainless steel and titanium are liked for the needles due to their durability and security. Uniformity in material selection aids in achieving harmony throughout all batches.
Accuracy Engineering
Precision design is essential in the production of derma rollers to make sure that each needle is straightened and formed precisely. This entails utilizing sophisticated machinery and proficient service technicians to keep the integrity of the roller design.
Standardized Production Processes
Carrying out standard manufacturing processes ensures that each derma roller is made with the very same degree of top quality. This includes establishing clear methods for assembly, evaluation, and product packaging.
Best Practice | Advantages |
---|---|
Product Selection | Guarantees toughness and safety and security |
Accuracy Engineering | Maintains design honesty |
Standard Processes | Guarantees uniformity and high quality |
Supplier Partnerships
Building solid partnerships with dependable suppliers is essential for maintaining high quality in derma roller production. Routine audits and high quality checks should be carried out to ensure that all materials fulfill the needed requirements.
Documents and Record Keeping
Thorough paperwork and record-keeping are necessary for tracking the manufacturing procedure and determining areas for enhancement. This practice helps with compliance with governing requirements and assists in keeping derma roller manufacturing standards.
Making Use Of Advanced Technology for Consistency
In derma roller production, adopting cutting-edge technology is essential to maintaining consistency and upholding high standards across every batch. The integration of advanced machinery and software streamlines the manufacturing process, ensuring precision in needle alignment, material handling, and quality control. These innovations not only enhance efficiency but also minimize errors, supporting the production of safe and effective derma rollers that meet rigorous regulatory requirements.
Automated Production Systems
Automated systems play an essential role in preserving derma roller manufacturing standards. These systems minimize human error, make sure uniformity, and increase production rate. By utilizing robotics and automated production line, producers can attain exact control over every aspect of the production process, from the alignment of needles to the safe and secure add-on of deals with.
Precision Engineering and Calibration
Advanced innovation permits accuracy engineering, which is crucial in the production of derma rollers. High-precision CNC devices and laser cutters ensure that each element is made to precise requirements. Regular calibration of these equipments is essential to keep accuracy and promote manufacturing requirements.
Real-Time Monitoring and Data Analytics
Implementing real-time monitoring systems allows manufacturers to effectively oversee the production process by leveraging sensors and IoT devices. These technologies gather critical data on parameters such as temperature, pressure, and operational speed. The collected data is analyzed in real-time to detect any deviations from established standards, facilitating immediate corrective actions to maintain consistency and quality in production.
Top Quality Assurance Through Advanced Testing
Advanced technology helps with extensive top quality guarantee screening. Non-destructive screening techniques, such as ultrasonic and X-ray inspections, can be used to detect any kind of defects or disparities in the derma rollers without creating damage. This makes sure that just items meeting the highest standards reach the market.
Combination of AI and Machine Learning
The integration of AI and artificial intelligence in the manufacturing process can better improve uniformity. These innovations can predict potential problems, maximize manufacturing schedules, and boost decision-making procedures. By evaluating historical data, AI systems can provide understandings into enhancing effectiveness and maintaining derma roller manufacturing standards.
Training and Development for Skilled Workforce
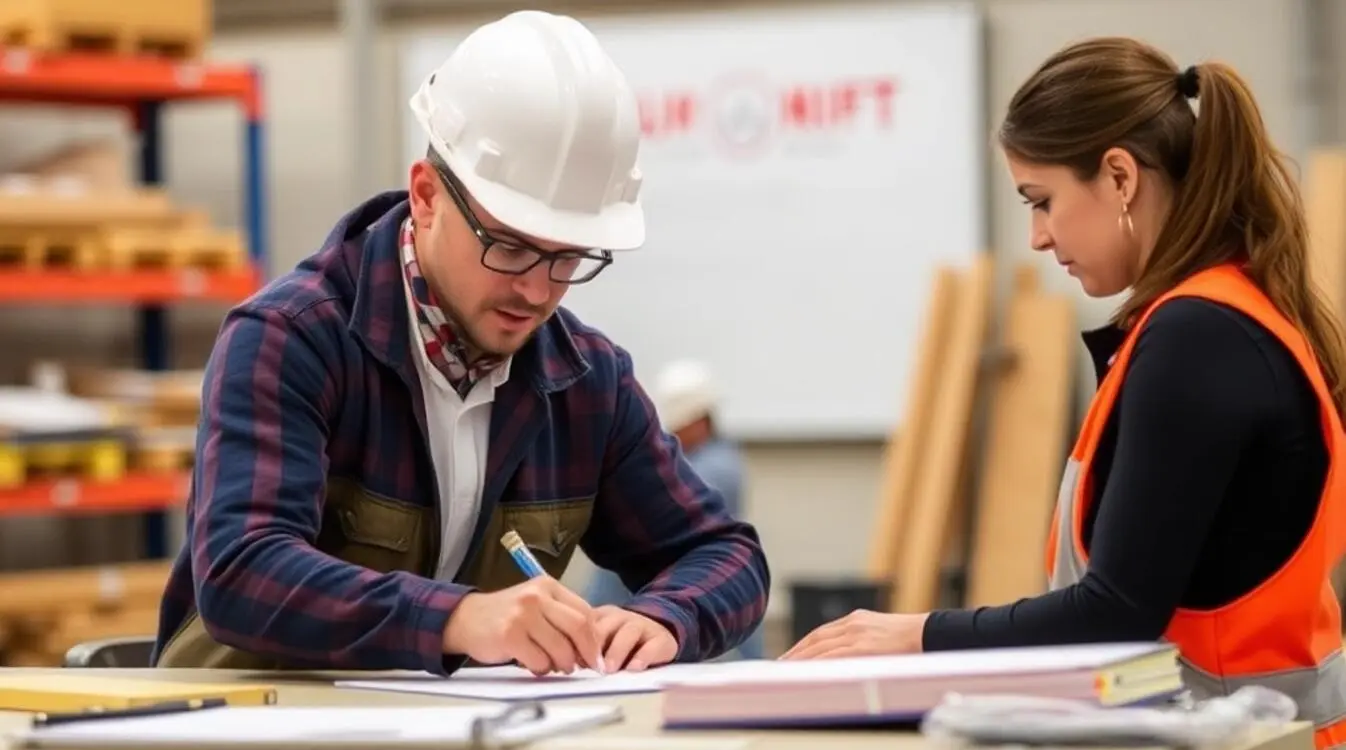
Relevance of Skilled Workforce in Derma Roller Manufacturing
Keeping derma roller production criteria calls for a very proficient workforce capable of performing exact jobs. The elaborate nature of derma roller production needs that each staff member is fluent in the specific needs and methods necessary to ensure consistency and high quality across every batch.
Comprehensive Training Programs
To achieve the highest criteria, it is critical to implement thorough training programs. These programs must cover:
Training Aspect | Summary |
---|---|
Technical Skills | Hands-on training in equipment procedure and upkeep. |
Quality control | Recognizing of high quality control measures and examination techniques. |
Security Protocols | Training in safety standards to stop mishaps and make sure work environment security. |
Item Knowledge | In-depth expertise of derma roller requirements and requirements. |
Constant Skill Enhancement
Recurring knowing is essential for maintaining derma roller production standards. Normal workshops and seminars ought to be performed to upgrade the workforce on the most recent industry trends and technical improvements. Urging participation in exterior qualification programs can improve the ability of employees.
Mentorship and Leadership Development
Developing a mentorship program can assist in nurturing future leaders within the company. Experienced workers can provide guidance and share insights with brand-new employees, fostering a society of constant improvement and quality. Management advancement initiatives can prepare staff members for future functions, ensuring a robust succession plan.
Performance Evaluation and Feedback
Routine performance assessments are vital for determining locations of enhancement and recognizing impressive contributions. Useful comments mechanisms can help employees straighten their work with the company’s purposes, therefore upholding derma roller manufacturing standards.
Regulatory Compliance and Certification Standards
Recognizing Regulatory Requirements
Maintaining derma roller production standards requires a comprehensive understanding of regulatory frameworks. Each country has specific guidelines that manufacturers must adhere to, ensuring both the safety and efficacy of the products. Familiarity with these regulations is critical to achieving compliance and upholding the integrity of every batch produced. This includes adhering to global standards like ISO 13485 for medical devices, FDA requirements in the United States, and CE marking regulations in Europe, each of which imposes rigorous checks on materials, manufacturing processes, and product testing.
Derma Roller Certification and Quality Assurance
Getting relevant qualifications is a vital component of adhering to derma roller manufacturing standards. Qualifications such as ISO 13485 for clinical devices and CE marking for European markets show a commitment to quality and safety and security. These qualifications require rigorous audits and paperwork, ensuring that all processes fulfill the essential criteria.
Documentation and Record Keeping
Comprehensive documentation and precise record-keeping are crucial for regulatory conformity. This consists of maintaining detailed records of materials, manufacturing procedures, and quality assurance steps. Appropriate documents assists in audits and supports constant renovation efforts by providing a clear background of producing methods.
Remaining Updated with Regulatory Changes
The regulative landscape is continually progressing, and staying informed regarding adjustments is crucial for preserving derma roller production criteria. Consistently examining updates from regulatory bodies and taking part in market discussion forums can help producers expect and adapt to new requirements, making sure ongoing conformity.
Involving with Regulatory Experts
Collaborating with regulative specialists can supply beneficial insights into conformity methods. These experts can supply guidance on browsing complicated regulations and aid in applying finest practices to fulfill certification criteria. Their experience helps in aligning production procedures with regulatory expectations, thereby boosting item quality and safety and security.
Constant Improvement Through Feedback and Testing
In the world of derma roller production, maintaining high standards in every batch is essential. Continual enhancement is an important part of this process, achieved with methodical feedback and extensive testing. This ensures that each item satisfies and goes beyond industry assumptions.
Significance of Feedback Mechanisms
Implementing efficient responses devices is essential for identifying locations of enhancement. Responses can be gathered from numerous sources such as consumer testimonials, employee understandings, and distributor analyses. By examining this information, manufacturers can pinpoint particular elements of the production procedure that call for improvement.
Structured Testing Protocols
Creating organized screening procedures is a foundation of preserving derma roller manufacturing standards. These procedures ought to include a series of tests, including:
Test Type | Objective |
---|---|
Material Quality Testing | Guarantees raw materials meet specified criteria |
Item Durability Testing | Evaluates the long life and robustness of the derma roller |
Safety Testing | Confirms that the item is risk-free for customer use |
Incorporating Feedback with Testing Outcomes
The assimilation of comments with testing end results is crucial. By correlating responses with test outcomes, makers can establish a detailed understanding of product efficiency. This enables targeted improvements, making sure that making requirements are constantly promoted.
Accepting Iterative Enhancements
Continuous enhancement is an iterative procedure. Producers should accept a cycle of screening, comments, and enhancement. This vibrant approach not only addresses present obstacles however also expects future requirements, fostering a society of quality in derma roller manufacturing.
Sustainable and Ethical Derma Roller Manufacturing Practices
In the realm of derma roller manufacturing standards, embracing sustainable and ethical methods is not only a moral responsibility but also a calculated advantage. As derma roller suppliers, we need to guarantee that our procedures decrease ecological effect while promoting the highest possible ethical standards. This strategy not only enhances our brand credibility but also meets the expanding consumer need for accountable production.
Ecological Impact Reduction
The key objectives in sustainable production is decreasing the ecological footprint. This can be achieved through the following procedures:
Strategy | Execution |
---|---|
Energy Efficiency | Using energy-efficient equipment and optimizing manufacturing timetables to decrease energy intake. |
Waste Management | Carrying out reusing programs and reducing waste via lean production strategies. |
Water Conservation | Adopting water-saving innovations and reusing water wherever feasible in the manufacturing process. |
Ethical Labor Practices
Maintaining ethical labor techniques is crucial in maintaining derma roller manufacturing standards. This includes ensuring fair salaries, risk-free working conditions, and appreciating workers’ civil liberties. Developing a clear supply chain and conducting normal audits can aid in keeping these requirements.
Responsible Sourcing
Choosing suppliers that comply with moral and sustainable techniques is crucial. By sourcing products sensibly, we can ensure that our items are premium quality and fairly produced. This includes validating that basic materials are obtained without exploiting labor or causing environmental harm.
Constant Improvement and Innovation
To maintain efforts aligned with derma roller manufacturing standards, it is crucial to nurture a culture of continuous improvement and innovation. Regular evaluations and updates to production methods, incorporating the latest sustainable technologies, ensure compliance with these standards while advancing ethical practices.
In summary, by embedding sustainable and ethical approaches into the production processes of derma rollers, we not only meet the established manufacturing standards but also contribute positively to society and the environment. This commitment to responsible manufacturing supports long-term success and strengthens our leadership in the industry.
FAQs on Maintaining Derma Roller Manufacturing Standards
What are the key derma roller manufacturing standards?
Derma rollers must comply with ISO 13485 standards for medical devices, ensuring safety, quality, and consistency. They may also require FDA approval, CE marking, or similar certifications depending on the market.
What materials are used in derma roller manufacturing to meet standards?
High-quality derma rollers are made with medical-grade stainless steel or titanium for needles and non-toxic, durable materials like ABS plastic or medical-grade polymers for the handles.
How do derma roller manufacturing standards ensure safety?
Manufacturing standards require rigorous testing for needle sharpness, material biocompatibility, and sterilization processes to ensure the product is safe for skin application.
Are there specific size requirements for needles in derma roller manufacturing standards?
Yes, derma rollers are typically manufactured with needle sizes ranging from 0.2mm to 2.5mm, and manufacturers must maintain precise consistency and quality control for these sizes.
What sterilization processes meet derma roller manufacturing standards?
Manufacturers use approved sterilization methods like gamma radiation, ethylene oxide gas, or autoclaving to meet sterility requirements outlined in industry standards.
Do derma roller manufacturing standards include packaging requirements?
Yes, standards require sterile, tamper-proof packaging, often produced in clean rooms compliant with ISO Class 7 or higher to prevent contamination during manufacturing and distribution.
What certifications indicate compliance with derma roller manufacturing standards?
Certifications such as ISO 13485, FDA approval, CE marking, and other region-specific approvals indicate adherence to manufacturing and safety standards.
Are derma rollers classified as medical devices under manufacturing standards?
Yes, derma rollers with needle lengths greater than 0.3mm are classified as medical devices and must comply with strict medical device manufacturing standards and certifications.
How do manufacturers test compliance with derma roller manufacturing standards?
Compliance testing includes biocompatibility testing for materials, durability tests for needles, sterility checks, and functional tests to ensure the product meets all safety and performance standards.
Do derma roller manufacturing standards require adherence to GMP guidelines?
Yes, manufacturers must follow Good Manufacturing Practices (GMP), which ensure proper documentation, controlled production environments, and consistent quality control.
References
- FDA, Quality System (QS) Regulation/Medical Device Good Manufacturing Practices, https://www.fda.gov/medical-devices/postmarket-requirements-devices/quality-system-qs-regulationmedical-device-good-manufacturing-practices
- BSI Group, ISO 13485: Medical Devices Quality Management Systems, https://www.bsigroup.com/en-GB/medical-devices/iso-13485/
- Europa EU, CE Marking for Medical Devices, https://ec.europa.eu/growth/sectors/medical-devices-new-regulations
- ISO, ISO Standards for Medical Devices, https://www.iso.org/standards.html
- CDC, Principles of Sterilization in Manufacturing, https://www.cdc.gov/infectioncontrol/guidelines/
- ASTM International, Biocompatibility Testing for Medical Devices, https://www.astm.org/medicaldevices/standards/
- UC Davis Food Safety, Key Materials in Dermaroller Manufacturing, https://ucfoodsafety.ucdavis.edu/
- OSHA, Material Safety and Handling Regulations for Medical Devices, https://www.osha.gov/
- Defense Acquisition University, Manufacturing Process Standards and ISO Compliance, https://www.dau.edu/
- Montana State University, Improving Safety in Medical Device Manufacturing, https://www.montana.edu/
- FDA, FDA Classification of Medical Device Standards, https://www.fda.gov/medical-devices/device-classes
- European Union Compliance, Principles of CE Marking for Dermaroller Exports, https://ec.europa.eu/growth/sectors/medical-devices-new-regulations
- ISO Insights, Advanced Techniques in Manufacturing Sterile Medical Devices, https://www.iso.org/standard/67179.html
- CDC, Quality Assurance and Testing for Medical Equipment, https://www.cdc.gov/medicaldevicesafety/
- UC Davis Food Safety, 3-A Sanitary Standards in Dermaroller Equipment, https://ucfoodsafety.ucdavis.edu/food-equipment-standards
- FDA, Standards for Non-Metal Materials in Medical Devices, https://www.fda.gov/medical-devices/device-labeling/nonmetal-materials