Table of Contents
ToggleBrief Overview of Derma Rollers
Derma rollers, highly acclaimed for their remarkable skin-rejuvenating capabilities, have become a staple in skincare routines worldwide. These handheld devices, which feature fine needles, actively gain reverence for their ability to induce controlled micro-injuries on the skin. This process triggers collagen synthesis and optimizes the absorption of skincare formulations. As the demand for derma rollers continues to surge, understanding the meticulous process of derma roller manufacturing is imperative. In this comprehensive guide, we provide an in-depth exploration of the intricate journey undertaken by derma roller manufacturers. Every aspect of the manufacturing process undergoes meticulous scrutiny, from selecting premium materials to implementing stringent quality control measures.
By delving into the nuances of derma roller production, both aspiring and established derma roller manufacturers can gain invaluable insights into optimizing their manufacturing processes. Whether it’s ensuring needle sharpness or adhering to regulatory standards, every step in the manufacturing journey contributes to delivering safe and effective derma rollers to consumers worldwide.
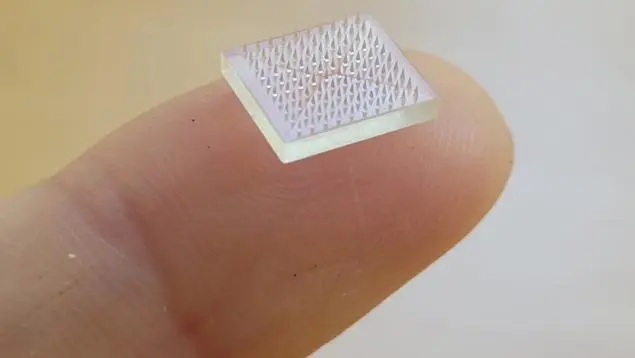
Importance of High-Quality Derma Roller Manufacturing in Skincare Products
The quality of manufacturing plays a crucial role in ensuring the safety and efficacy of skincare products like derma rollers. High-quality manufacturing processes utilize premium materials, stringent quality control measures, and adherence to industry standards to produce reliable and durable products.
In the case of derma rollers, using top-grade materials for needles and handles is essential to prevent skin irritation or infections during use. Poorly manufactured derma rollers may have uneven needle lengths, blunt tips, or improper sterilization methods that can lead to adverse effects on the skin.
Investing in high-quality manufacturing not only enhances the performance of derma rollers but also instills trust among consumers regarding product safety and effectiveness. Skincare enthusiasts rely on well-manufactured products for consistent results without compromising their skin’s health.
Understanding Derma Rollers
The Marvels of Derma Rollers: A Skin-Care Revolution
Micro-needle rollers, also known as derma rollers, actively represent relatively new skincare devices used to boost skin recovery and achieve a radiant, smooth, and youthful look. They consist of compact handheld instruments with a fixed handle and a revolving tip containing micron-sized hypodermic needles.One of the main goals of derma rollers is to induce microscopic wounds at the facial skin surface and to cause the skin to trigger its own protective and renewing response through the production of collagen.
Unlocking the Mechanism: Overall Overcoming the Derma Roller Deep Treatments Transform Your Skin
The powerful impact of derma rollers actively comes from the way they stimulate the skin’s built-in mechanism for healing after damage. Like things’ imperceptible fineness, when the clockwise needles smoothly take the skin surfaces, they cause the microchannels to deepen and make the skin surface covered with skin care products. This process, which is micro-needling, not only amplifies product penetration but also actively boosts collagen and elastin production.
The Science Behind Microneedling: Collagen Induction Therapy
This procedure uses a device that creates tiny needle-like punctures in the skin to stimulate collagen production, leading to tighter and smoother skin.
The roller mechanism that stimulates collagen production and other dermal components, such as hyaluronic acid, makes derma rollers the best home remedy for skin challenges and deficiencies. Collagen is a main protein in the dermis layer that contributes to the characteristics of supple, smooth, and youthful-looking skin. The dermarollers, when broken into smaller injuries, transmit a response to your body to boost the rate of collagen production, thus serving to smoothen and firm skin while revealing a youthful look later in life.
Beyond Skincare: Treating Various Skin Concerns with Derma Rollers
Derma rollers can be considered multifaceted tools that are able to appeal to a broader range of esthetic needs than just anti-aging support. They have demonstrated good efficiency in decreasing acne scars, hyperpigmentation, and stratch marks, and even promoting hair growth throughout the scalp. This device restores cells’ regeneration in affected areas while supporting the circulatory system, enhancing comprehensive remedies, and thus addressing diverse dermatological issues.
Safety First: Instructions On the Dermaroller Use
If you make use of derma rollers for proper skin renewal, they offer numerous benefits, but you should be aware of the negative effects if you are not careful. Cleaning the roller appropriately every time, picking up the right length of needles for the specific expectations, and expert advice are central when the roller is part of your skin care regimen. The safety of your skin should weigh more on the scale, so find the best balance with desirable outcomes.
Raw Material Selection for The Production of the Dermal Roller
The Kind of Needles Inserted in Dermarollers Could Be Provided
Derma rollers largely rely on the quality of the materials used in their production. An integral piece of a derma bead is the needle, which can be of different types and materials. Derma roller manufacturers regularly use titanium and stainless steel as materials for this particular type of derma roller needle.
Stainless steel needles are hard and economically valid; for them, there are significantly more manufacturers available. On the contrary, customers prefer titanium needles for their strength and high resistance to rust, making them an ideal choice for those sensitive to metals or allergic to certain metals.
Considerations for Handle Materials
Adding to the needle, the materials for the handle are also essential parts of derma roller production. Frequently, handles are covered in materials like plastic and medical silicone. Plastic handling is quite lightweight and cheap. However, it has a shorter shelf life in comparison with silicone handles. Clinical-quality Siiil-con silicon handles feel comfortable in your hands, and you have a sense of control over the roller while maneuvering on the skin, which provides a good gliding sensation.
Options for Efficiency and Safety Efficiency in Design
Needle Length and Density
The existence and frequency of the needles on the derma roller either contribute to the efficiency of the operation or imperil it. Tiny needles are a good choice for the initiator or people who are sensitive to the needles, and they should use needles that are longer (1.0mm–2.0mm) for more effective therapy. Pastry rollers may densely pack their needles. On one hand, using rollers with greater density actively prevents overspreading, which, on the other hand, may cause discomfort in the absence of proper operation.
Stable and Spherical Shape of the Roller Head
The size and shape of the roller head give the roller different abilities on the areas of skin where it is most comfortable. Bigger roller heads cover more surface area in fewer strokes and therefore become a preset for fatty areas like the thighs and stomach. On the other hand, small roller heads are more effective for applying foundation around the eyes or the lips due not only to their size but also to their “delicacy.”.
The purpose of implementing quality control in manufacturing is to reduce defects and enhance the production of products of adequate quality.
Manufacturers need to comply with tight quality control norms throughout the production stage, whether items meet industry requirements or not.
Sterilization Processes
Sterilization actively ensures that derma rollers remain uncontaminated and that the skin remains free from infection during therapy. Adhering to the guidelines set by industry standards and regulations will provide a solid foundation, guaranteeing a safe and satisfying air travel experience.
All the producers need to adhere to the regulatory deadlines and particular guidelines outlined by the health authorities for product safety and labeling.
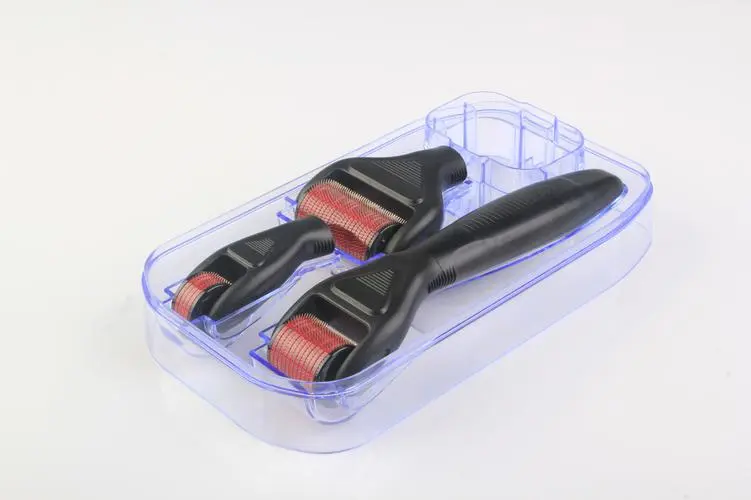
Novel Approaches in Producing Derma Rollers Using Technological Advances
Automation in Derma Roller Manufacturing Processes
When it comes to derma roller manufacturing, automation has turned out to be a game-changer, largely displacing the old production processes by virtue of the emerging efficiencies and precision of production. Today, the use of automation by derma roller producers has become a popular move to eliminate labor-intensive processes, which in turn helps improve efficiency and product quality.
Automation in the production lines has actively changed numerous aspects of production, including error control mechanisms and the overall uniformity of productivity. Overcoming the challenges of automatic needle making and troubling assembly allows robotics and machinery to process tasks such as needle production, handle fabrication, and assembly with unparalleled accuracy and speed.
Adapting new technologies, such as automation, in particular, can assist derma roller manufacturers in reaching good productivity rates while maintaining high quality control standards. Automated systems guarantee the constant observation and adjustment of production conditions, even in such minute detail as each derma roller, to meet product specifications with the highest accuracy.
Not only does automation feature as a crucial factor in smart energy production, but it also facilitates resource optimization and minimizes waste during all stages of the production cycle as well. This outcome is critical as it facilitates material usage control and downtime reduction, which can potentially save manufacturing costs and enhance manufacturing efficiency.
Automation, in the long run, has immensely affected the manufacturing industry of derma rollers. As processes become more efficient and elaborate, manufacturers produce higher-quality products, leading to increased output. With the improvement of technology, we assume that automated joining of derma rollers will only increase manufacturing capabilities, pushing the limits even further in the field of skin care.
Automation of Production Lines in Factories Will Result In the Following Positive Outcomes
The use of automatic production lines in the manufacture of derma rollers is accompanied by some key benefits that consumers and manufacturers alike can enjoy. The adaptability of the qualitative scale of operations thanks to automation is another advantage, enabling the generation of higher volumes of the product without affecting the quality.
In addition, automated systems accelerate the manufacturing process significantly, which usually results in a decrease in the amount of time required for raw material procurement to finished product assembly. This productivity stems from the compressed production cycles, which bring the additional bonus of a price tag that is likely to be cheaper than that of competing brands while still maintaining product quality.
Benefits of Automated Production Lines
The technological environment of the derma roller manufacturing industry has evolved much in recent generations with the advancements in equipment and capabilities, which have actually changed the standards considerably. What was unthinkable decades ago is now possible with laser-guided needle insertion systems that maximize the precision with which the needles are placed on nickel rollers, resulting in consistent depth and alignment across each and every nut produced.
Besides that, clever and intelligent sensors integrated into manufacturing equipment enable in-process monitoring of such parameters as pressure and temperature that lead to the optimization of process control and the assurance of product quality. The key elements that are part of the advancements here are algorithms for artificial intelligence (AI) that suggest the maintenance schedule for the machine component before the actual problem happens, making the production online and error-free all the time.
Technological Advancements in Derma Roller Manufacturing Machinery
The machining modus operandi of derma roller manufacturing exhibits a rapid transformation in technology that has reached a peak and is beyond human comprehension. Innovative inventions like modern-level needle positioning systems that use lasers to place needles onto roller heads have reshaped the manufacturing process. Today, such systems allow for a predictable depth and alignment of needles across all the units produced.
Moreover, smart sensors embedded into the busy equipment allow for the direct monitoring and adjusting of conditions such as pressure and temperature in real time. Consequently, both process control and product quality assurance are elevated to a higher level. The development of these technologies relies in part on AI algorithms, which enable the generation of condition-based maintenance plans for machinery components. This proactive approach addresses potential meltdowns and ensures the continuous operation of production cycles.
Furthermore, 3D printing technologies have actively catalyzed previously unthinkable possibilities in derma roller customization. Now, manufacturers can actively tailor rollers more accurately to specific client needs without compromising the flexibility of the designs. These technological inventions not only improve the efficiency and accuracy of the production processes but also create the possibility of introducing novel ideas for product development in the skincare industry by means of creative boundary detachment.
As a result, producers of derma rollers have a larger base of advanced manufacturing technologies at their disposal, meaning that they are ready to manufacture products that present precision engineering quality at its highest standard while meeting the evolving consumer demands for effectiveness, safety, and reliability. Automation brings efficiencies that, coupled with last-gen technology, drive the emergence in the manufacturing process of a new epoch and era where innovation brings new breakthroughs from the realization of the idea to product distribution.
Specialized Coatings on Needles for Enhanced Performance
Manufacturers apply specified surface coatings to needles to achieve maximized functionality and other goals. Another prominent factor that differentiates good-quality skin needles from others is the finishing coatings applied to the needles. These films of multiple layers take up an essential position in boosting the capacity and functionality of the derma roller. Among the coatings, titanium, with its lifetime performance and biocompatibility, is taken to be the best.
Titanium-coated needles are durable against corrosion, keeping their sharpness properties for many repeats. This allows for a pleasurably consistent and efficient microneedling experience. Not only do manufacturers use titanium in the manufacturing of derma rollers, but they can also add coatings like gold or platinum to the rollers to benefit the users.
The needles coated with gold allegedly might have anti-inflammatory effects, thereby making them perfect for acute types of skin. Platinum paints possess microbial growth-inhibiting effects, actively reducing the likelihood of infections being contracted during microneedle treatments.
The specially made coatings do not only raise productivity but also accompany the most luxurious and advanced skincare for people with premium taste. In addition, factors like hydroxyapatite and diamond-like carbon (DLC) are frequently use in the process of coating on the Derma roller (nanotechnology).
Hydroxyapatite coating has a positive impact on collagen and assists in skin smoothness; this is the main reason it is used a lot in anti-aging treatments. The DLC coatings give the objects excellent hardness and durability through all the mechanical loading conditions without losing needle sharpness or suffering from misshape.
Customization Options for Branding and Packaging
In the present-day business landscape, branding and packaging have escalated to a crucial factor in product selection by consumers, and they have become a way of distinguishing the product from its competitors. Derma roller manufacturers provide many customization services through which brands can create package designs that show their own true branding if they wish to. Brands can get very specific when it comes to detailing colors and finishes. For the purpose of aligning with the brand’s strategy, manufacturers can actively add other techniques, such as logo printing or embossing.
Such companies have come up with packaging designs that go beyond just changing the trademarks. Some manufacturers even offer private labeling, where brands can create their own device or add their brand names to that of the manufacturer, as well as put their logos on the package. This high degree of product differentiation helps customers recognize the brand and build a relationship that is based on a product that they recognize among the many choices available.
Not only that, but customization is also essentially the bundling of a derma roller along with respective skincare products or accessories designed for certain glowing skin problems or going on therapies. Through specially designed ranges targeted at different skin issues, such as extra-large pores and those with wrinkles and fine lines, companies can position themselves as comprehensive and reliable brands without compromising on the customers’ variety of needs.
Explain the Next-Level Quality Assurance and Testing Exercise Procedures
Inspection Techniques Violate The Product’s Quality
In derma roller manufacturing, product quality is paramount to retaining customer confidence and loyalty because they are the sources of regulatory authorities as well. In order to obtain the goal, manufacturers use a ceiling-to-floor inspection from the beginning of production. Visual inspection, where experts take time to examine each part of the PRP, keeping in mind any errors or inappropriateness, is one of the initial steps of inspection.
For instance, we will be looking for uniformity of the needles, the handle grip for strength, and adjusted alignment of the parts put together. Besides the measure, the dimensional verification of derma rollers is used to ensure that all products meet exact specifications.
This process incorporates custom-made calipers, rulers, and micrometer measurements to accurately determine the length of the needle, roller head dimensions, handle ergonomics, and so on. The slightest deviations from the prescribed values of the machine can result in improper operation or the risk of injury during skin manipulations.
Manufacturers also test microfunctions, which make certain devices run smoothly and without mechanical flaws. The materials also play a critical role in the quality control of derma roller manufacture; this is another very important factor.
In this process, we actively test the raw materials from which we make the needles (stainless steel) and tubes (ABS plastic) for their strength, toughness, and biocompatibility. We conduct tensile strength tests on needles and other materials to ensure they can withstand multiple uses without bending or breaking. Additionally, we perform biocompatibility tests to determine whether the materials are safe for contact with human skin.
Clinical Testing for Efficacy and Safety
In these experiments, subjects who agree to use the rollers in instructional form are recruited, and the duration of the research is controlled to gauge success. Dermatologists meticulously scrutinize participants’ skin reactions, textures, and even alterations in appearance, as well as any adverse effects that may develop during or after treatments.
Efficacy research is conducted to prove that the use of the derma roller is beneficial for eliminating skin problems such as acne, wrinkles, pigmentation, and untoned marks on the skin. Researchers can quantify the effectiveness of derma rollers by measuring parameters such as fibroblast collagen production level, skin firmness, hydration levels, and overall improvement in the skin condition before and after rolling.
In clinical trials, researchers actively conduct sterility checks to assess any side effects or reactions associated with microneedle usage. They actively monitor sensitive areas, prone to irritation and redness, for signs of irritation, inflammation, or infection. This active monitoring allows for the prompt identification of any adverse responses to treatment.
The Role of Investigation and Quality Control in Derma Roller Manufacturing
Every reported complaint or out-of-the-ordinary situation undergoes close investigation to determine its relation to the product or other factors. First and foremost, the companies demonstrate their commitment through the active participation of two key departments, namely manufacturing and clinical teams. As part of their dedication, the manufacturers have established robust quality control and inspection processes, which, along with thorough clinical testing protocols, aim to ensure that every derma roller produced on the manufacturing line meets stringent standards.
The evidence of beneficial efficacy influences users to trust the products that are being provided by the manufacturers. Healthy and quality products develop through continuous commitment, double-standard verification by the manufacturers of the workers, and laboratory investigations to ensure quality, safety, and efficacy.
The company produces skincare products with specific necessities in mind, targeting their intended client base. The main advantage of these holistic principles is that consumers are sure to enjoy peace.
Last but not least, confiding in the roller derived from dermal production is necessary.
Environmental Sustainability Practices in Derma Roller Manufacturing
Eco-Friendly Materials Used in Production
Sustainable production of dermarollers has been increasingly becoming responsible, and responsible production of dermarollers has actually been anticipated. In recent times, industry players have turned to bio-based and/or recyclable materials to minimize their ecological footprints during the creation phase.
Laboring on the eco-friendly part of the derma roller production, there are organic biocompatible polymers from renewable plant-based sources as raw materials. These bioplastics offer a viable alternative to the traditional ones and help reduce the carbon footprint that comes with manufacturing.
Apart from this, a handful of visionary brands are taking into account bamboo handles for dermal rollers since they are eco-friendly and accurate to the earth. Bamboo is a rapidly growing stemless plant that can be planted in any soil quality without the need for watering or the application of pesticides, which makes it an environmentally friendly replacement for handles.
To manufacture bamboo-based derma roller, companies can produce an item that will not only be effective in hair loss mitigation but will meet the sophisticated tastes of environmentally conscious clients. Subsequently, dedrome roller production has come to incorporate substantial amounts of recycled materials in order to adopt classic environmental recycling principles and circular economy strategies.
These newly recycled plastics obtained from post-consumer waste are being used as the key components of the derma rollers, which decreases the dependency on virgin plastics and helps them stay out of landfills. This eco-friendly approach thereby saves natural resources and even helps to avert pollution—plastic pollution, which is a burning environmental issue the world is facing today.
Waste Management Strategies Within The Manufacturing Process
An appropriate waste management system is in essence the most vital factor, which all the steps along the derma roller manufacturing process must apply to reach environmental sustainability. Extensive recycling activities are widely viewed as a logical and indispensable practice by conscientious manufacturers, and ensuring advanced recycling programs is a core part of their approach.
Man victories will be achieved by the fact of separation of the different types of waste—to be more specific, the sorting of the plastic scraps, packaging materials, and all this waste is not recyclable—which will lead to process simplification and the reduction of the produced waste going to the landfill.
Additionally, a few ahead-questioning corporations have incorporated closed-loop systems into their manufacturing operations to maximize efficiency and reduce waste. In a closed-loop machine, products or excess substances generated throughout production are gathered, processed, reintegrated, and returned into the manufacturing cycle anywhere possible.
This round technique allows for reduced uncooked cloth consumption, power utilization, and the normal environmental impact associated with derma roller production. Furthermore, waste reduction tasks, which include lean manufacturing ideas, were followed by using many manufacturers to optimize operational efficiency while minimizing pointless useful resource intake.
Lean practices focus on figuring out inefficiencies in manufacturing methods, putting off wasteful practices, and constantly improving workflows to increase productivity while lowering the environmental footprint. By embracing lean methodologies, derma curler manufacturers can acquire cost savings along with environmental advantages through streamlined operations.
Legal Regulations and Compliance Standards
The Foundation of Safety: Guide to FDA Regulations for Derma Roller Manufacturers
When it comes to manufacturing derma rollers, adherence to regulatory standards is paramount for ensuring product safety and efficacy. In America, the Food and Drug Administration (FDA) plays a vital role in regulating skincare products, which include derma rollers.
Manufacturers have to comply with FDA guidelines to make certain that their products meet quality standards and are safe for patron use. One of the key factors in FDA policies that derma curler manufacturers need to adhere to is labeling.
The FDA calls for each skincare product, together with derma rollers, to have accurate and transparent labeling that includes information about elements, usage instructions, warnings, and capability aspects. This allows purchasers to make informed choices about the products they use on their skin and ensures product safety.
In addition to labeling necessities, the FDA also mandates Good Manufacturing Practices (GMP) for skincare product manufacturers. GMP suggestions define the important tactics, tactics, and documentation needed to make certain that skin care merchandise is always produced and managed consistent with satisfactory standards.
Ensuring Product Excellence and Safety: The Role of FDA Compliance in Derma Roller Manufacturing
Derma roller manufacturers need to adhere strictly to these recommendations to uphold product excellence and safety. Furthermore, the FDA regulates certain ingredients utilized in skin care merchandise, such as derma rollers.
Manufacturers need to ensure that their products do not contain prohibited or limited substances that would be dangerous or pose risks to customers’ fitness. By following FDA policies related to component safety and regulations, derma curler manufacturers can exhibit their commitment to generating terrific and secure merchandise.
Compliance with FDA regulations is non-negotiable for derma roller manufacturers seeking to bring safe and effective products to market. By following hints related to labeling, GMP practices, component safety, and different regulatory necessities set forth by the FDA, manufacturers can build trust with purchasers and prioritize product first-class in an increasingly competitive marketplace.
Global Reach: International Standards for Exporting Derma Rollers
As the skin care industry continues to grow globally, derma curler manufacturers have to now not only follow home regulations but also navigate global requirements when exporting their products across borders. Understanding those worldwide standards is crucial for ensuring smooth market access in exceptional areas while maintaining consistency in product quality.
One distinguished worldwide standard relevant for exporting derma rollers is ISO 13485:2016: Medical Devices, Quality Management Systems, and Requirements for Regulative Functions. This preferred system specifies necessities for a nice management system wherein an enterprise needs to demonstrate its potential.
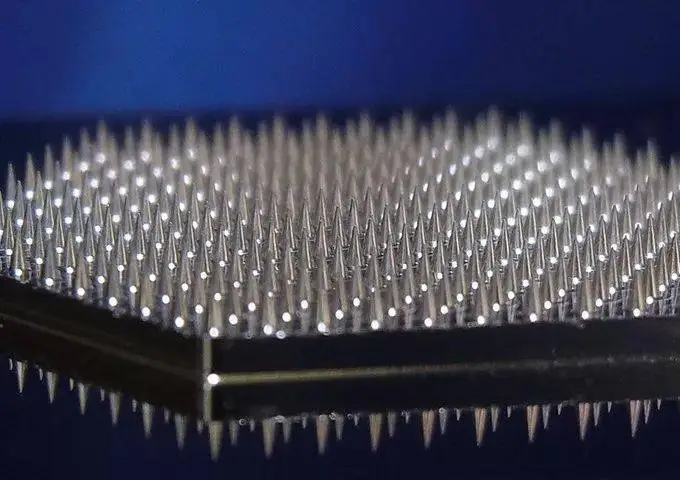
The Future of Derma Roller Manufacturing
Innovation and technological Advancements
The future of derma curler production is poised for big technological advancements and innovation. Manufacturers are making an investment in research and development to enhance product capabilities, including clever derma rollers with integrated microsensors that can analyze pores and skin conditions in real-time. The integration of AI and gadget learning algorithms is also revolutionizing the customization alternatives available to purchasers, bearing in mind personalised skincare answers tailored to a man’s or woman’s needs.
Sustainable Practices and Eco-friendly Materials
As environmental sustainability takes precedence throughout industries, derma curler manufacturers are increasingly adopting eco-friendly materials and sustainable practices in their manufacturing methods. From utilising biodegradable needle substances to implementing strength-efficient manufacturing strategies, the future of derma curler manufacturing is focused on reducing its carbon footprint while nevertheless delivering remarkable products.
Global Expansion and Market Growth
With the rising demand for skin care merchandise globally, the derma roller market is projected to revel in a tremendous boom within the coming years. Manufacturers are increasing their operations globally to attain a much wider purchaser base and tap into rising markets. Strategic partnerships with dermatologists and skincare professionals are also becoming more common, similarly solidifying the position of derma rollers in expert skin care treatments.
Enhanced Safety Standards and Regulations
The future of derma curler manufacturing will see a continued emphasis on safety requirements and regulatory compliance. With an increasing recognition of client protection and product efficacy, producers are making an investment in rigorous checking-out methods and first-rate warranty measures. Collaborations with regulatory bodies to establish industry standards will make sure that derma rollers meet all vital necessities for secure usage.
Conclusion
The future of derma roller production holds sizeable promise for clients and industry stakeholders alike. With ongoing improvements in technology, a focal point on sustainability, global marketplace enlargement, and stringent protection rules, the panorama of derma rollers is evolving into one that prioritizes innovation and great. As we look ahead to what lies beyond the horizon of skin care innovation, we can be positive about the transformative capacity that awaits us inside the realm of derma curler manufacturing.
Reference:
- From Xdermaroller Manufacturing, The Best Derma Roller Manufacturer I Ever Met, Dec 26, 2023
- Leonna Dsouza, Vivek M. Ghate, and Shaila A. Lewis, Derma rollers in therapy, Published online 2020 Oct 26. doi: 10.1007/s10544-020-00530-3
- Written by VICTORIA HOFF, UPDATED ON 08/22/23 02:30PM, Reviewed by LUCY CHEN, MD /Board-Certified Dermatologist, Fact checked by ANNA HARRIS, Dermarolling 101